The system is processing. Please wait a moment!
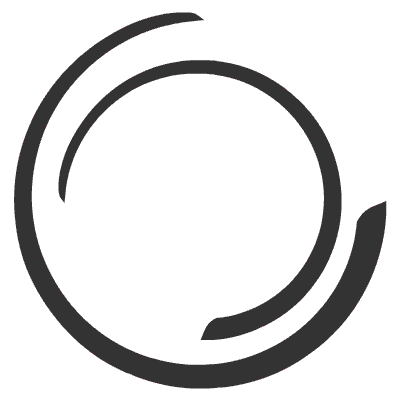
Vui lòng lựa chọn loại báo giá!
- Home Product CONTAINSER HOUSE & OFFICE Nhà Trọ Bằng Container
Prefabricated Boarding House
TABLE OF CONTENTS
- What is a prefabricated boarding house?
- Current need for boarding houses?
- Should we build prefabricated boarding houses or not?
- Compare prefabricated and traditional boarding house construction
- Some models of prefabricated boarding houses today
- Some of the most beautiful prefabricated container house models today
Building prefabricated boarding houses is becoming a popular trend today thanks to its outstanding advantages compared to traditional boarding houses. This prefabricated boarding house model is specially designed for rent, to provide comfortable and economical accommodation for students and workers. Flexibility in construction and low investment costs make prefabricated boarding houses an ideal choice for many investors. Along with that, the ability to quickly construct and easily move and upgrade also increases the appeal of this type of boarding house, meeting the increasing needs of the modern rental market.
.jpg)
What is a prefabricated boarding house?
Prefabricated boarding houses are an advanced type of housing model, built according to the principle of prefabricated houses, bringing many outstanding advantages compared to traditional boarding houses. The structure of the prefabricated motel includes elements designed to be easily assembled and disassembled, allowing for flexibility in moving and reusing when needed.
Prefabricated motels often use lightweight but durable materials such as steel, aluminum, corrugated iron, and soundproof and heatproof panels. These materials not only help reduce the overall weight of the building but also ensure sustainability and energy efficiency. High-quality soundproofing and heat-insulating materials help maintain a comfortable living environment, minimize noise and effectively regulate temperature.
SEE MORE ARTICLES
20 newest Container house models this year
Refer to the 50 most beautiful smart prefabricated house models!
The prefabricated boarding house model is widely deployed in areas with high housing demand, such as industrial parks, construction sites, and city suburbs. This provides a convenient and cost-effective accommodation solution for workers, pupils, students and those in need of temporary accommodation.
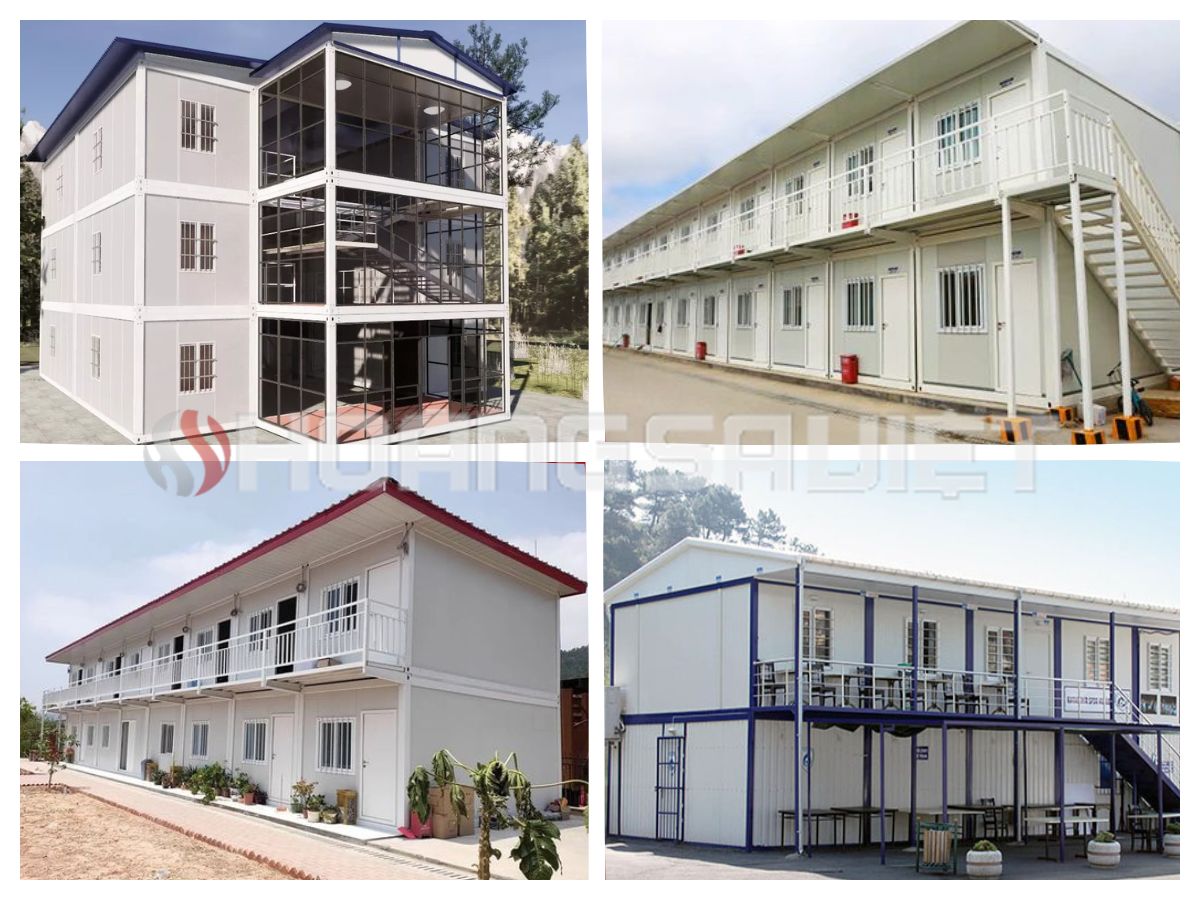
Not only flexible and cost-effective, prefabricated boarding houses can also be customized according to the user's needs. With the ability to assemble quickly and not requiring complicated construction steps, prefabricated motels help reduce construction time and costs. Boarding house elements can be mass-produced at the factory, then transported and assembled on site, ensuring precision and high quality.
SEE MORE PRODUCTS:
Prefabricated accommodation is also environmentally friendly thanks to the use of recycled materials and reduced construction waste. When no longer needed, these structures can be dismantled and reused in another location, minimizing negative impacts on the environment.
Prefabricated boarding houses can now be designed in many different sizes and designs, meeting a variety of user needs. A special feature of this model is that all parts of the house such as walls, partitions, steel frames, doors, ceilings, and floors are pre-manufactured at the factory. This helps ensure consistent quality and saves construction time.
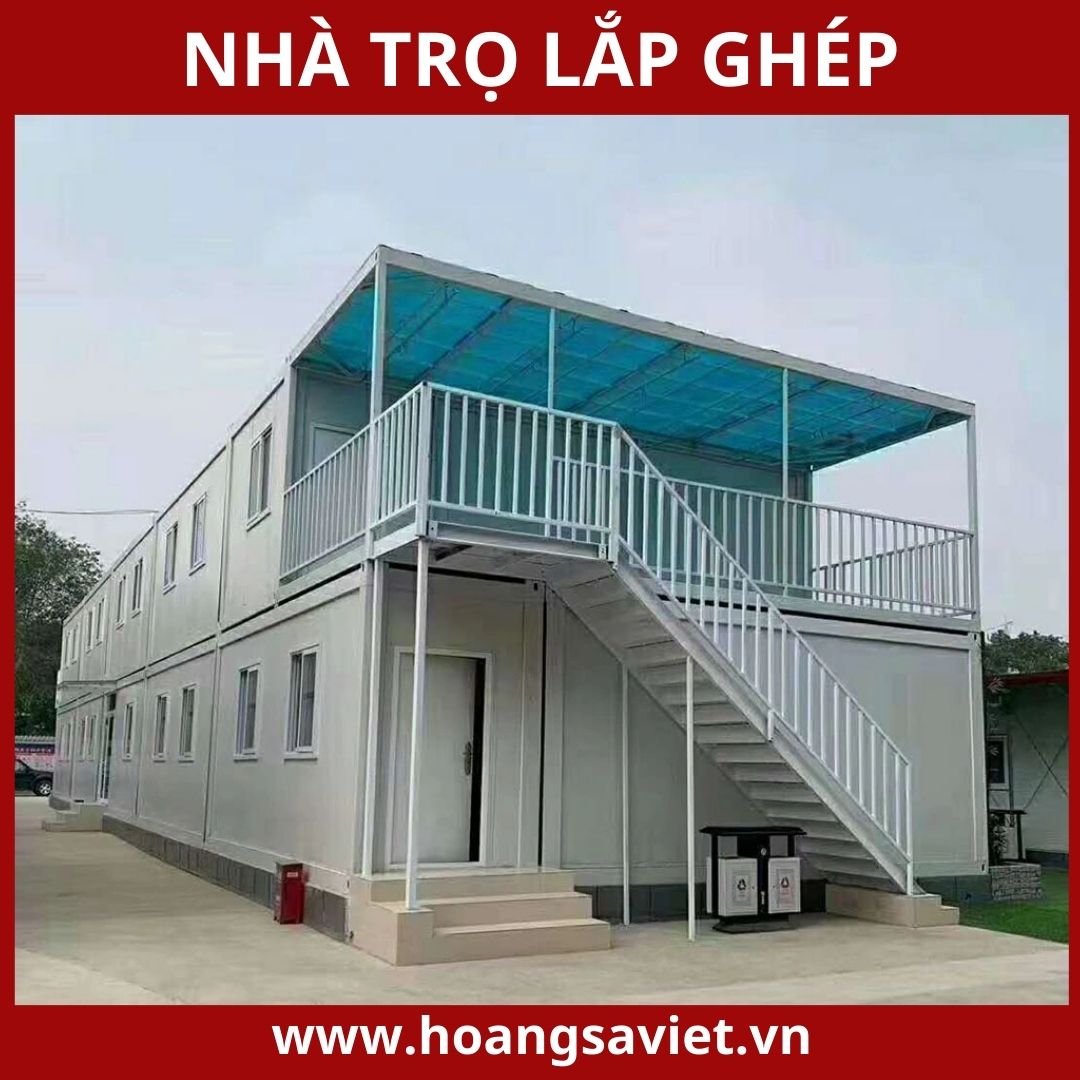
When customers need to build a prefabricated house , these parts will be transported to the installation location requested by the customer. The on-site assembly process is quick and efficient, not only helping to minimize construction costs but also bringing maximum convenience to users. Components are precisely designed and finished at the factory, ensuring high quality and quick assembly.
Prefabricated motels can also be customized to suit specific customer requirements, from room size and style to color and finishing materials. This brings maximum flexibility and comfort, helping users make the most effective use of space.
With outstanding advantages such as flexibility in design, quick construction, and guaranteed quality, prefabricated boarding houses are becoming a popular trend in the modern construction industry, meeting diverse accommodation needs. and brings many practical benefits to users.
SEE MORE PRODUCTS:
Current need for boarding houses?
Not only in big cities but even in small towns and cities, the need for accommodation is always great. Renting affordable accommodation is always the optimal solution for people with low income.
With the increasing demand for boarding houses, many people have found this to be a stable and safe source of profitable investment. Owners of vacant land or long-term leased land have begun to consider building boarding houses or boarding houses with many rooms to meet the needs of tenants. Investing in boarding houses not only helps maximize the value of real estate but also brings sustainable profits in the long term.
By building boarding houses, investors not only contribute to solving the accommodation needs of a large population but also contribute to promoting local economic development. The prefabricated boarding house model is becoming a popular choice because of its quick construction time, low investment costs and flexible customization ability, meeting all requirements from tenants.
SEE MORE ARTICLES
20 newest Container house models this year
Refer to the 50 most beautiful smart prefabricated house models!
Boarding houses assembled with lightweight, durable materials such as steel, aluminum, corrugated iron or soundproof and heat-insulating panels not only bring comfort to tenants but also ensure sustainability and safety in use. The quick and easy installation process saves time and costs, while also facilitating management and maintenance.
Thanks to its outstanding advantages, the prefabricated boarding house model is increasingly attracting the attention of many investors, becoming a perfect solution to meet the increasing demand for accommodation in modern society.
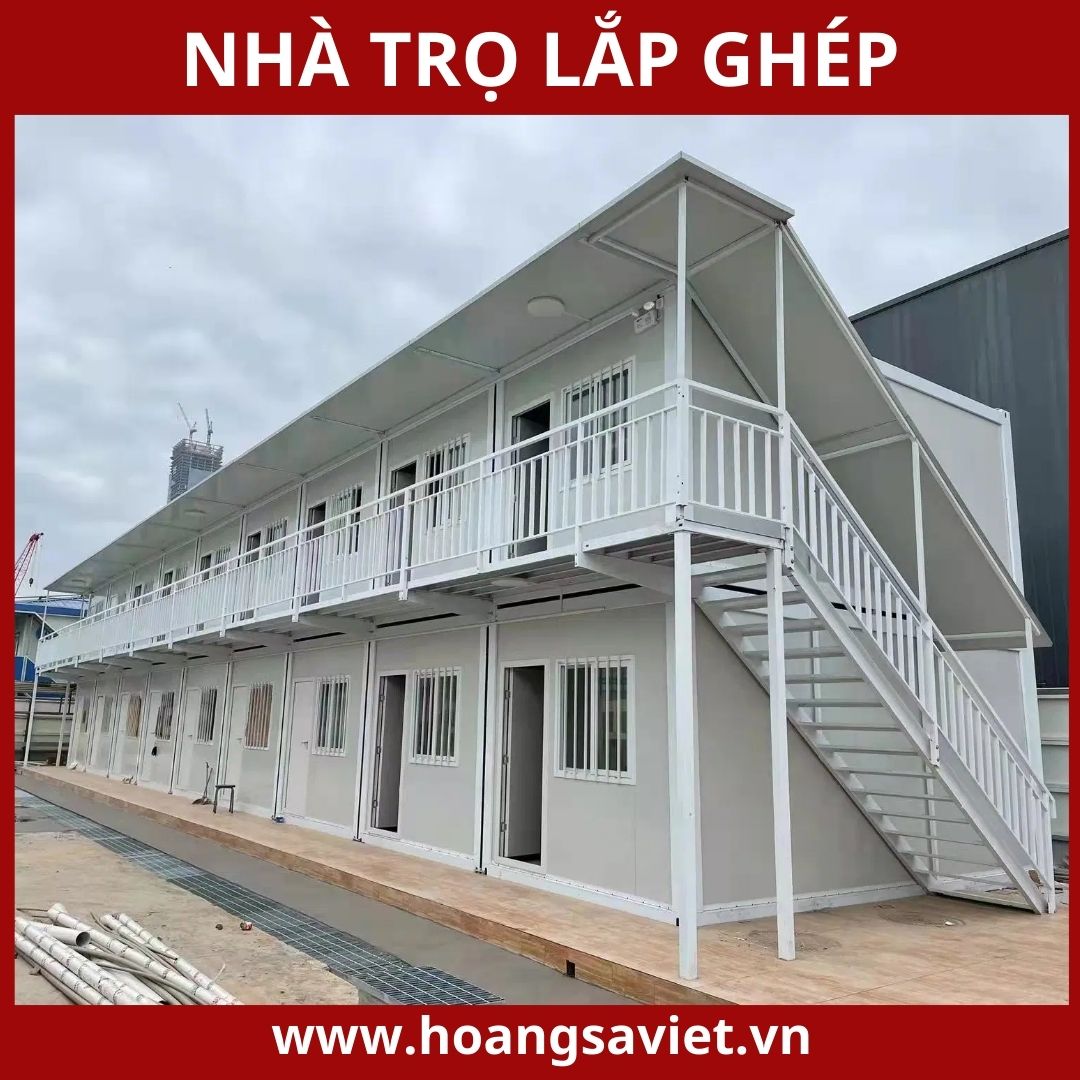
Should we build prefabricated boarding houses or not?
Although prefabricated boarding houses are still new to many people, they have proven to be highly applicable in various fields such as construction works, factories, restaurants, and homestays. When it comes to using prefabricated houses for rent, many people are still hesitant, thinking that this type cannot be compared with traditional houses in terms of durability, soundproofing, and heat insulation...
In fact, prefabricated boarding houses are increasingly asserting their superiority. With modern technology, materials used for prefabricated houses such as steel, aluminum, corrugated iron, and soundproofing and heat-insulating panels are strictly tested, ensuring high quality and durability. These materials not only provide stability but also help minimize the impact of weather, creating a comfortable living environment for tenants.
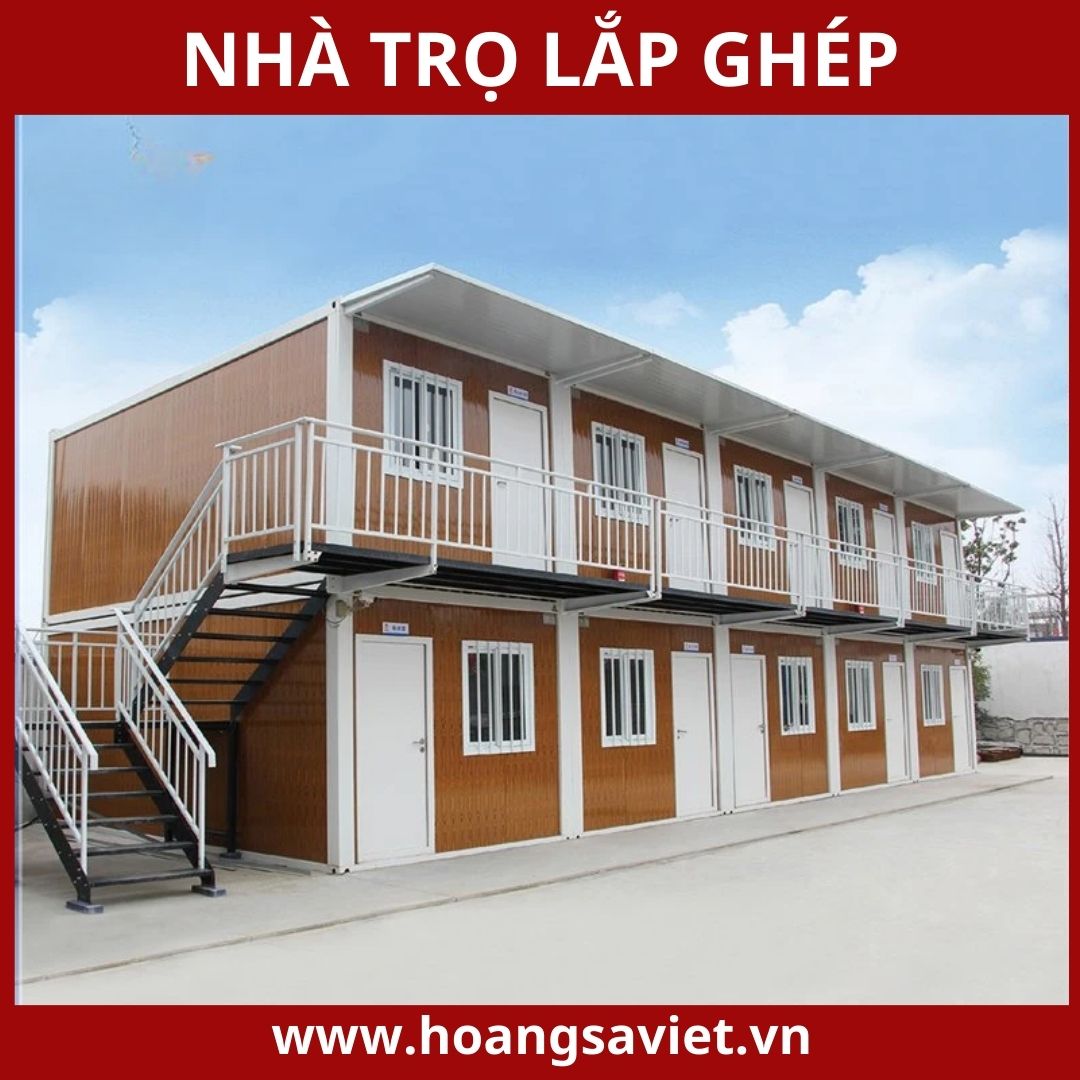
Not only stopping at durability, prefabricated motels also excel in flexibility. Parts of the house such as walls, partitions, steel frames, doors, ceilings, floors... are all pre-manufactured at the factory, then quickly transported and installed at the desired location. This not only saves construction time but also reduces costs compared to traditional houses.
In addition, the easy and quick assembly makes prefabricated motels an ideal solution for areas with high demand for accommodation such as industrial parks, export processing zones, or crowded labor concentration areas. activists and students. Prefabricated boarding houses also offer flexibility in design, easily adjusting size and style to suit the specific needs of each target group.
Thanks to its outstanding advantages in durability, soundproofing, heat insulation, and flexibility in design, prefabricated boarding houses are gradually gaining the trust of many investors and tenants. This is not only a cost-effective solution but also a sustainable, modern choice that satisfies accommodation needs in the context of increasingly rapid urbanization.
SEE MORE PRODUCTS:
Compare prefabricated and traditional boarding house construction
The comparison of prefabricated boarding house construction and traditional cement boarding house construction can be made based on the following factors:
Construction cost:
Prefabricated boarding house:
One of the outstanding strengths of prefabricated boarding houses is that construction costs are often lower than traditional houses. This is thanks to the use of lightweight materials such as steel, aluminum, and soundproof and heat-insulating panels. These materials not only help reduce the load on the project but also significantly save on transportation and construction costs.
The prefabricated motel assembly process is designed to be simple and efficient, with components pre-manufactured at the factory. This helps shorten construction time compared to building from start to finish using traditional methods. Once the parts are transported to the installation site, the assembly process is quick and easy, without requiring a lot of labor or complicated techniques.
SEE MORE ARTICLES
20 newest Container house models this year
Refer to the 50 most beautiful smart prefabricated house models!
On-site installation also brings many economic benefits. Because the parts have been precisely manufactured and quality tested before leaving the factory, installation only needs to be carried out according to predetermined steps without many obstacles. This helps reduce labor costs and minimize errors and incidents during construction.
Taken together, thanks to the optimization of the production and installation process, the prefabricated motel not only saves construction costs but also brings high efficiency in time and resources. This is the ideal choice for those who want to invest in a boarding house business model with a reasonable budget and quick completion time.
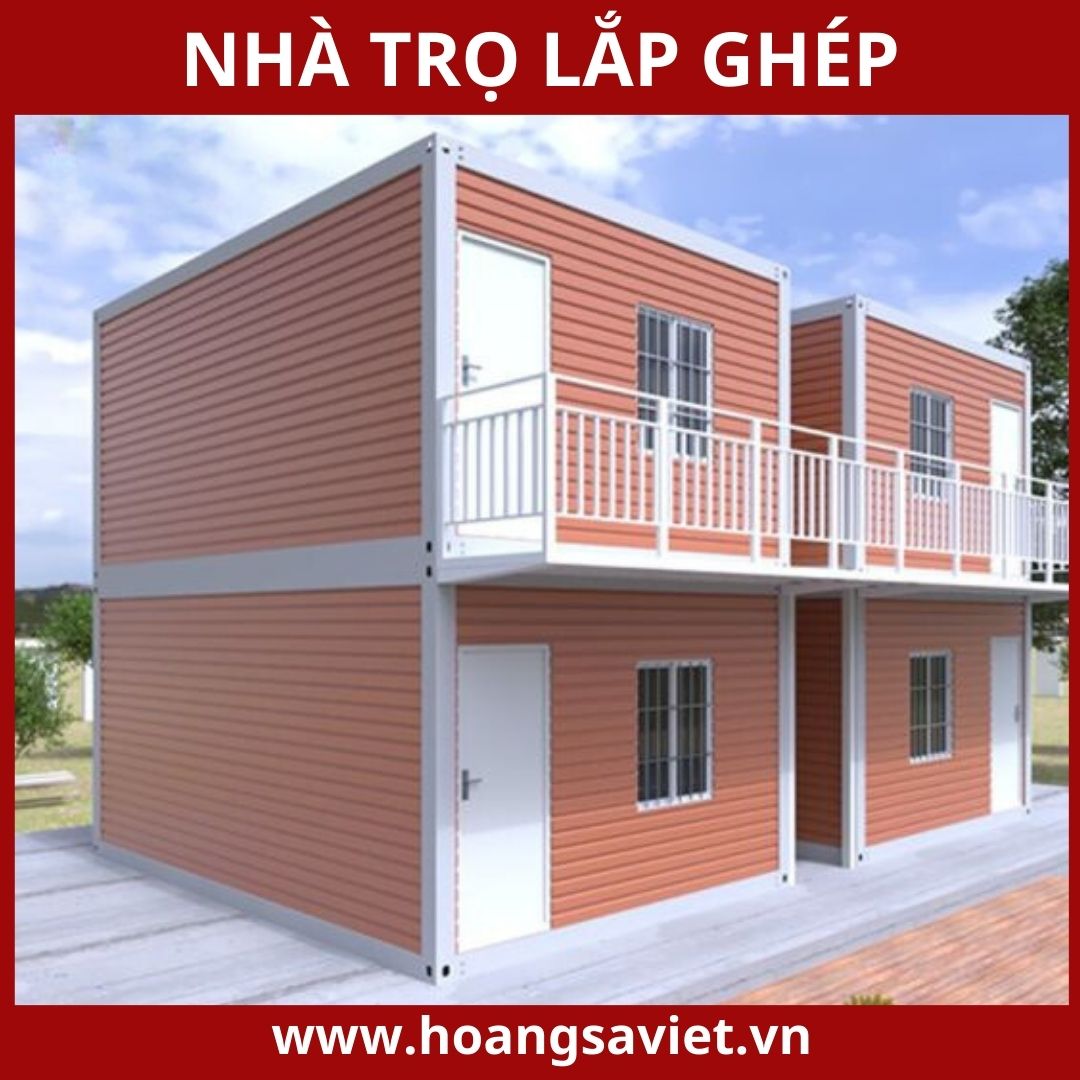
Traditional cement inn:
The cost of building a traditional cement motel is often significantly higher due to the use of heavy materials such as cement, sand, gravel, and bricks. These materials are not only more expensive but also require more complex transportation and handling processes, increasing the total investment cost.
The process of building a traditional cement boarding house includes many detailed steps, from digging the foundation, pouring concrete, building walls, pouring floors, installing electricity and water systems, to finishing stages such as paint walls, tile and install windows and doors. Each step requires high technology and the participation of many groups of skilled workers, from builders, carpenters, electricians to plumbers.
SEE MORE ARTICLES
20 newest Container house models this year
Refer to the 50 most beautiful smart prefabricated house models!
Due to the complexity of the construction process, the construction time of traditional boarding houses is often long, requiring strict management and continuous monitoring to ensure construction quality. Long construction time along with high demand for human resources and techniques not only increases labor costs but also creates pressure on schedule and budget.
Although the initial cost is higher, traditional cement inns are highly appreciated for their durability and bearing capacity. However, the cost and construction time requirements make this model a less attractive option for investors who want a quick and cost-effective solution.
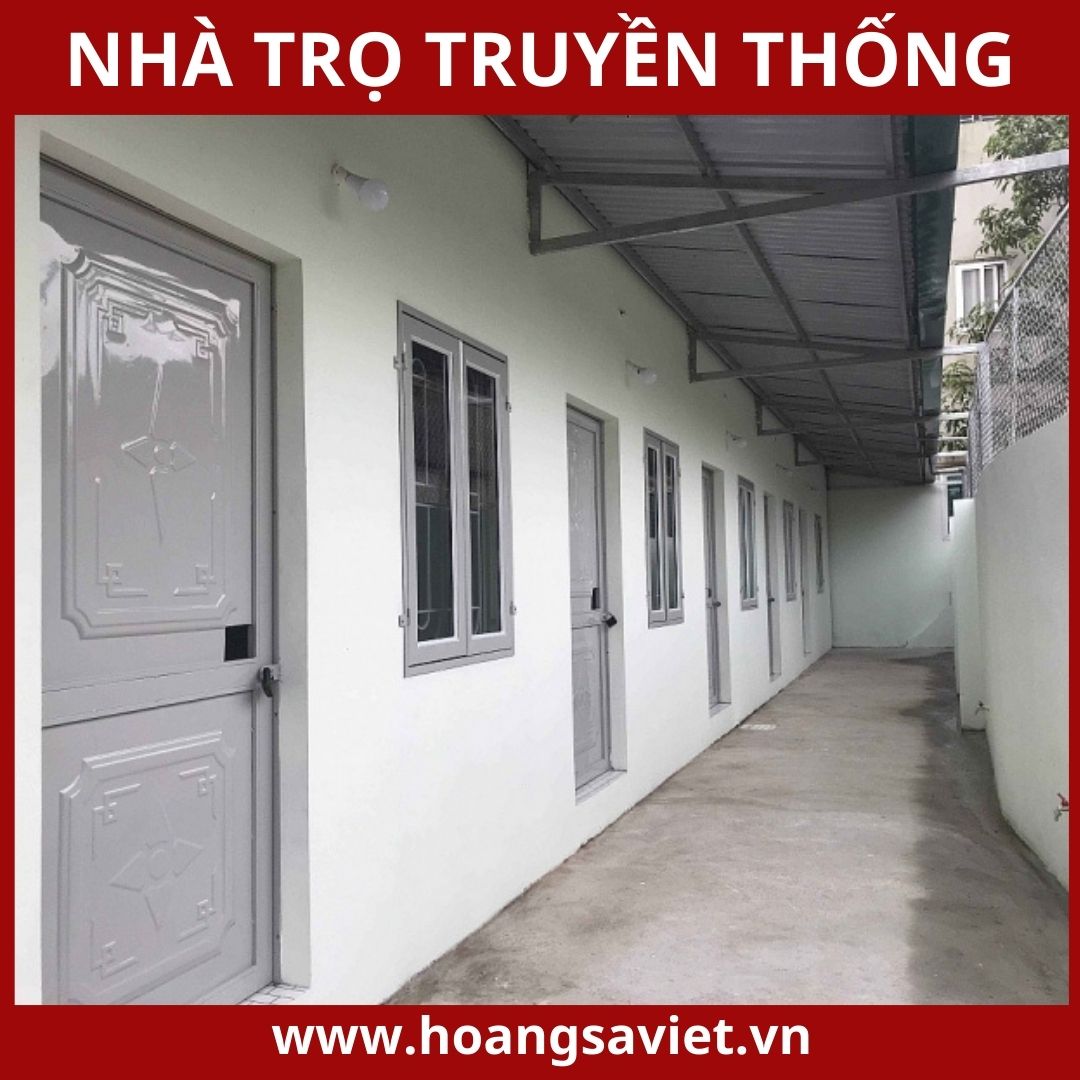
Construction time:
Prefabricated boarding house:
Prefabricated boarding houses have outstanding advantages in terms of construction time. Thanks to the parts of the house being pre-manufactured at the factory, the on-site construction process becomes much faster and more convenient. Assembly of pre-prepared parts significantly reduces construction time compared to traditional methods.
This process not only simplifies construction steps but also reduces complexity in project management. Materials such as steel frames, soundproofing and heat-insulating panels are precisely cut and machined at the factory, then transported to the installation site and assembled according to available designs. This not only ensures high accuracy but also minimizes errors during construction.
SEE MORE ARTICLES
20 newest Container house models this year
Refer to the 50 most beautiful smart prefabricated house models!
Quick construction time helps save labor costs and reduce additional costs arising from project prolongation. This allows investors to quickly put the project into use and start earning profits from rentals as soon as possible.
In addition, prefabricated motels can be easily expanded or changed in structure when needed. Flexibility in design and assembly is also an important factor that helps prefabricated motels become an attractive choice for investors who want to optimize construction time and costs.
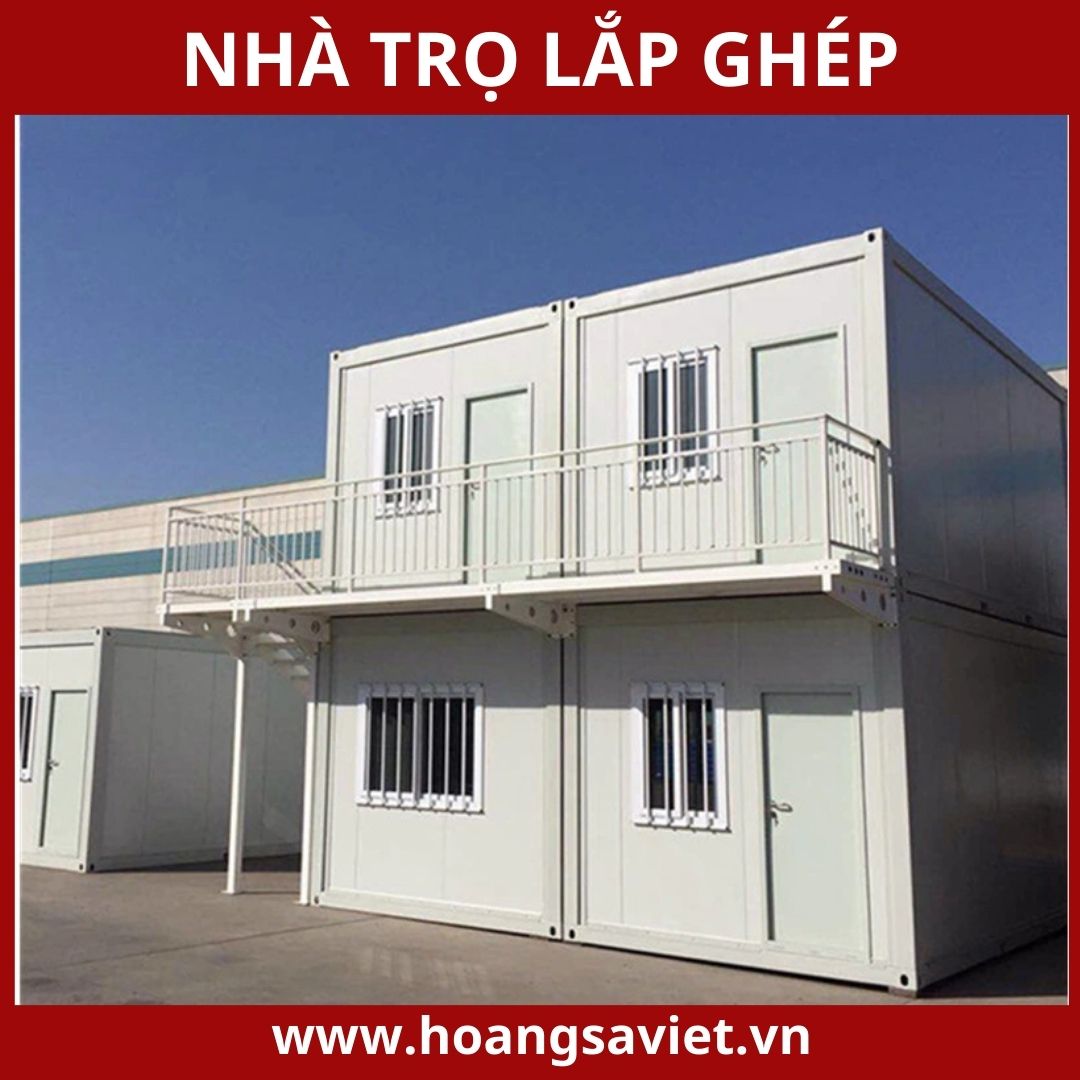
SEE MORE PRODUCTS:
Traditional cement inn:
Building a boarding house with traditional cement often takes more time than the assembly method because it requires many complicated steps. From building the foundation, framing the structure, building walls to the finishing stages, all require considerable time and effort.
The construction process of a traditional cement inn usually begins with foundation construction, a step that requires waiting time for the cement and concrete to completely dry before continuing with subsequent construction work. After that, framing the structure and building walls must also follow the process of waiting for the material to dry and stabilize before proceeding with the next steps.
SEE MORE ARTICLES
20 newest Container house models this year
Refer to the 50 most beautiful smart prefabricated house models!
These stages not only require time but also hard work and patience from construction workers. Having to wait for the material to dry and harden sufficiently before continuing work not only increases construction time but also increases labor and project management costs.
However, despite the longer construction time, traditional cement inns are often appreciated for their durability and stability after completion. The sturdiness and reliability of this construction is often the preferred choice of investors who want to ensure the sustainability of their assets.
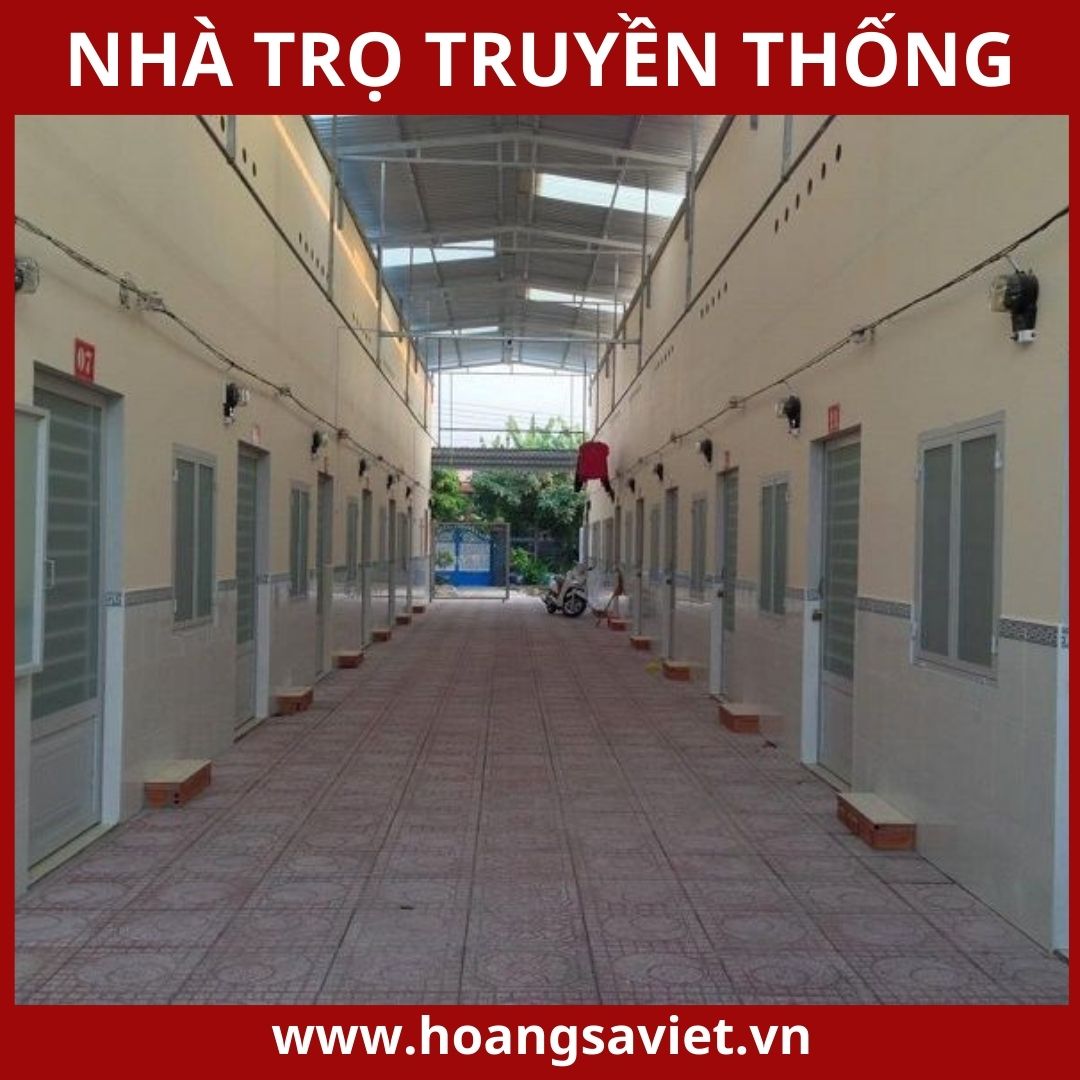
Durability and maintenance:
Prefabricated boarding house:
Prefabricated boarding houses use materials such as steel, aluminum and soundproof and heatproof panels, creating diversity and flexibility in design and structure.
Thanks to the use of these modern materials, prefabricated motels are often highly durable and require little maintenance. The materials do not rot or fade over time, helping the project maintain its beauty and solidity over the years.
The stability and durability of prefabricated motels not only bring financial peace of mind to investors but also increase the value of the property in the long run. This makes prefabricated accommodation an attractive option for business projects such as rentals or homestays.
Traditional cement inn:
Boarding houses built from traditional cement are often highly durable, especially when built with quality technology and materials. However, to maintain this durability, owners need to regularly perform maintenance measures.
Because they are subject to weather and environmental influences, cement motels often require regular maintenance. Tasks such as repainting the surface, waterproofing and repairing cracks are things that need to be done periodically to ensure the sustainability and aesthetics of the boarding house.
Proper care and maintenance will help extend the life of the building, minimize repair costs and maintain a safe and comfortable living environment for residents.
SEE MORE PRODUCTS:
Flexibility and extensibility:
Prefabricated boarding house:
Prefabricated boarding houses not only bring convenience in initial construction but also flexibility in expanding and changing design according to user needs. With a structure that can be easily dismantled and reassembled, parts of the inn can be flexibly moved and reused in new locations. This provides flexibility and diversity in optimizing living and working spaces, while also saving costs and time compared to rebuilding from scratch.
Traditional cement inn:
Expanding and adapting the design of the traditional cement inn faces many difficulties due to its fixed structure. When you want to expand or change, you often have to carry out many complicated steps such as demolishing old parts and rebuilding from scratch. This process is not only costly and time-consuming but also requires careful preparation and clear planning.
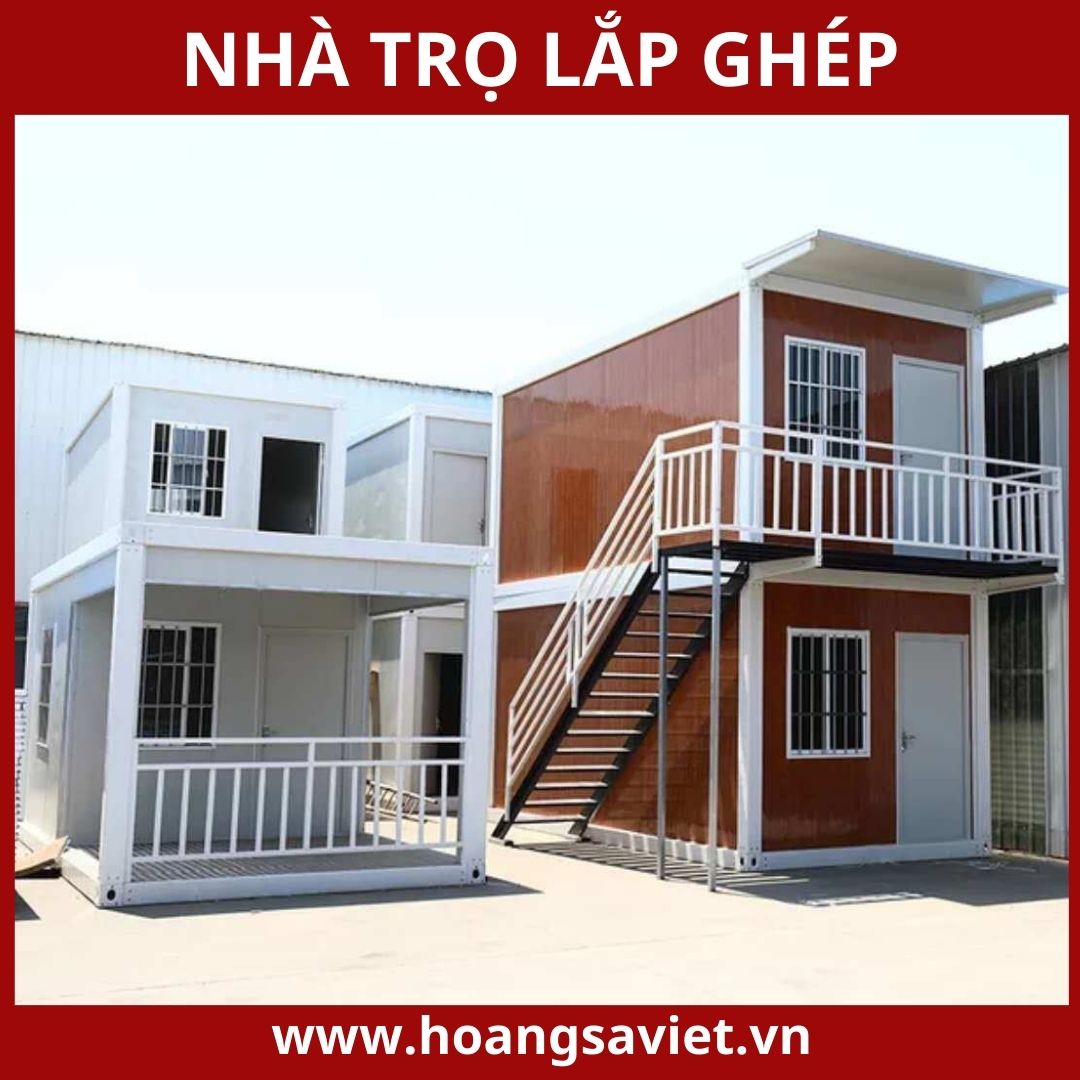
Sound and heat insulation:
Prefabricated boarding house:
Thanks to the use of soundproof and heat-insulating panels, prefabricated boarding houses can significantly improve living conditions for residents. However, it is worth noting that the quality of the soundproofing and thermal insulation properties will depend on the type of material used in the manufacturing and installation process.
Traditional cement inn:
With thick walls and sturdy structures, traditional cement inns often have better soundproofing and heat insulation than other types of inns. However, to achieve optimal performance, attention must be paid to the use of additional heat and sound insulation materials.
Aesthetics:
Prefabricated boarding house:
With a modern and diverse design, prefabricated boarding houses provide flexibility for investors to customize according to specific preferences and needs. This allows for many different styles and colors to be combined, creating rich and unique options.
Traditional cement inn:
With a classic design, traditional cement inns create sturdy and beautiful buildings. However, changing the design and color is often more complicated than a prefabricated motel , requiring more attention and effort during the implementation process.
Some models of prefabricated boarding houses today
Currently, there are a variety of prefabricated boarding houses on the market, suitable for the different needs and financial conditions of each region. Below are some popular and popular prefabricated boarding house models at the present time:
1-storey prefab house
Single-story prefabs are a flexible and convenient option for providing temporary housing during construction sites, special projects, or areas requiring mobility. Typically, these boarding houses are designed to meet the short-term needs of workers, engineers, or employees participating in large construction projects.
Although there is only one floor, the prefabricated boarding house still provides a comfortable and convenient living space for users. Constructed from lightweight materials such as steel and acoustic and thermal insulation panels, they are capable of providing the necessary protection in all weather conditions.
With high mobility, one-story prefabricated motels can be easily moved and installed at different locations depending on usage needs. This saves time and costs on construction, while providing flexible accommodation solutions for workers and employees during construction and engineering projects.
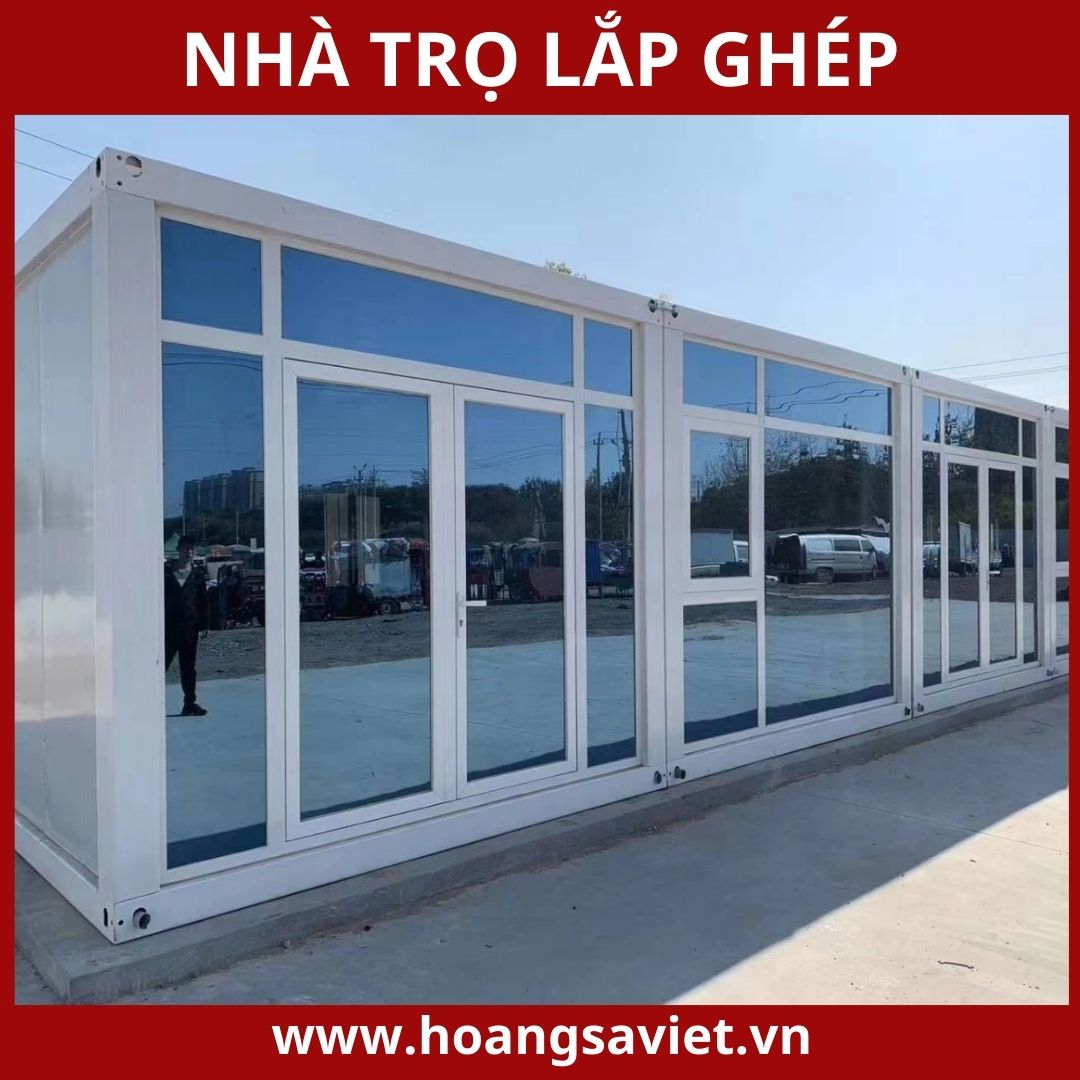
2-storey assembled boarding house
The 2-storey prefabricated boarding house is a flexible and effective solution for temporary housing construction, especially in industrial construction projects or areas requiring flexible mobility. This type of boarding house is often built from lightweight materials such as steel frames, panel walls, or containers.
One of the great advantages of a 2-storey prefabricated boarding house is cost savings during the construction process. Compared to traditional boarding houses, the cost of building a 2-storey prefabricated house is often significantly lower. The production process of house parts is carried out on a mass production line, helping to reduce time and costs. After that, these parts only need to be transported to the construction site and assembled to form a complete house.
These 2-story motel models not only bring convenience and cost savings, but can also be designed in many different styles and sizes to meet customers' specific needs. From compact models for areas with limited space to larger variations for large projects, 2-storey prefabricated boarding houses meet many different needs and requirements of the market.
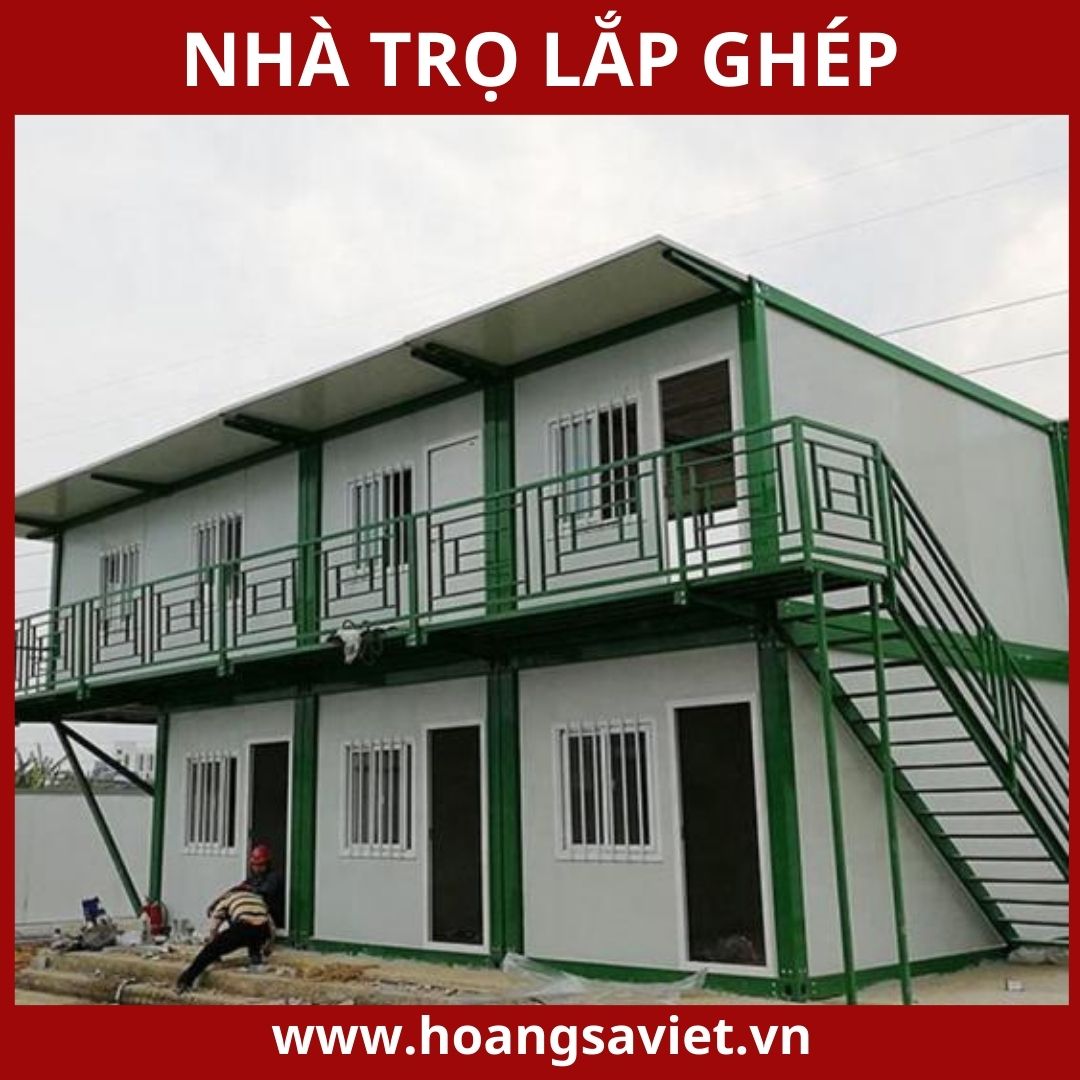
SEE MORE PRODUCTS:
3-storey prefab house
The 3-storey prefabricated motel is a flexible and economical construction innovation that uses pre-manufactured components and then assembles them at the construction site to create a three-storey building.
For those who are interested in the economic and time aspects of construction, the 3-storey prefabricated boarding house model brings many benefits. Instead of having to spend time and effort on the building process from scratch, using pre-manufactured parts helps reduce time and costs. This also provides design flexibility, allowing customization to the customer's specific needs.
However, during project implementation, ensuring the stability and safety of the structure is a top priority. Therefore, a detailed and careful plan is required from project planning to the assembly stage, to ensure that the building meets technical and safety standards during use.
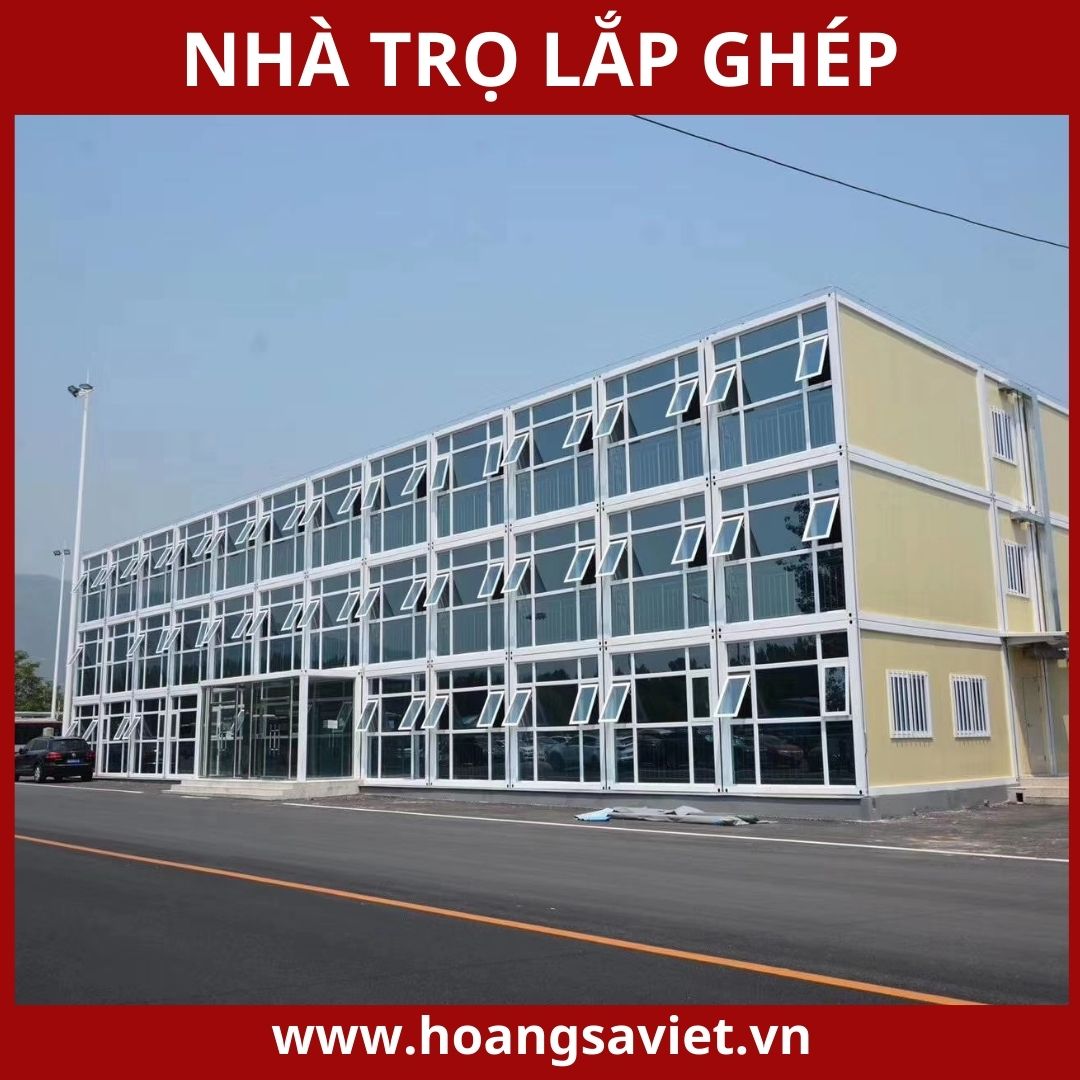
Some of the most beautiful prefabricated container house models today
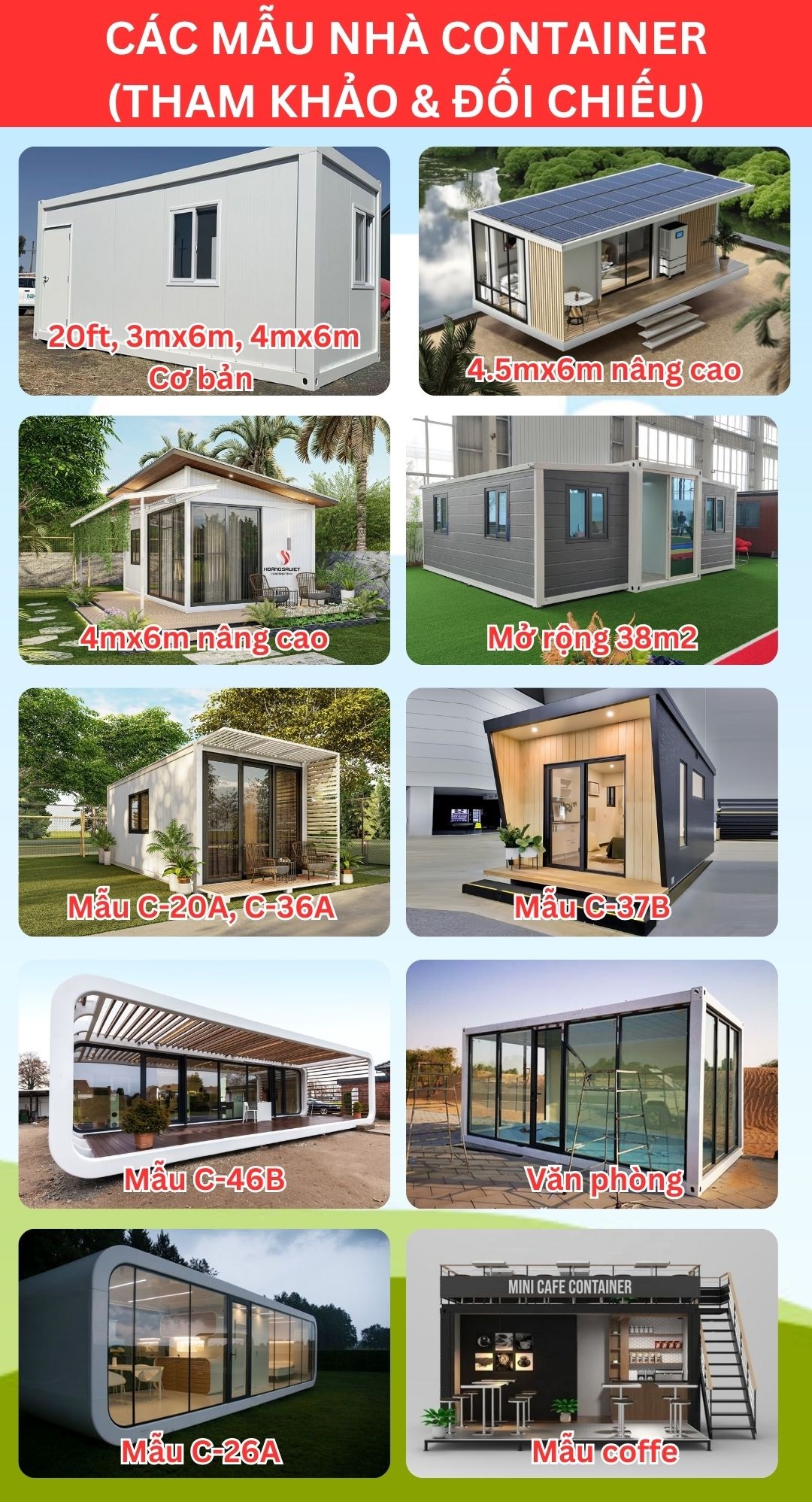
SEE MORE PRODUCTS:
Hiện chưa có đánh giá nào về sản phẩm này!