The system is processing. Please wait a moment!
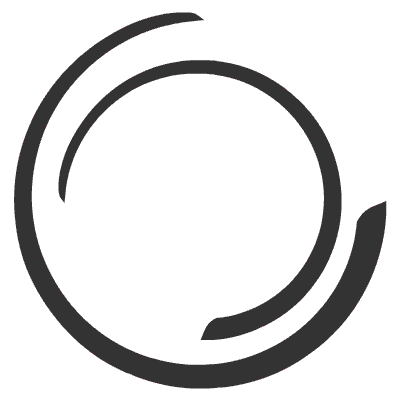
Vui lòng lựa chọn loại báo giá!
- Home Product prefab modular house
Prefabricated Warehouse
Code: NK
- Unit price: 1M2 (from 2.8-3.8 million/m2)
- The above price does not include interior design and tempered glass installation
- Model: Warehouse (NK)
- Origin: Vietnam
- Brand: Hoang Sa Viet Construction
- Frame material: U160mm steel, 2.5mm thick, tempered - electrostatic
- Wall material: Specialized 50mm Panel with 2 layers of Glasswool
- Insulation ability: 95%
- Fire resistance: 100%
- Connection type: Smart Connector
- Electrical system: Basic (LED lights, sockets, CB)
- Warranty: 10 Years
TABLE OF CONTENTS
- WHAT IS A PREfabricated WAREHOUSE? FUNCTION OF STEEL FRAME WAREHOUSE
- BASIC STRUCTURE OF A PREfabricated WAREHOUSE
- BASIC EQUIPMENT REQUIRED IN THE WAREHOUSE
- WHY IS THIS THE PRIORITIZED SOLUTION, WHAT ADVANTAGES DOES IT HAVE?
- CONSTRUCTION PROCESS OF PREfabricated WAREHOUSE
- WAREHOUSE INSTALLATION WHICH LOCATIONS SHOULD BE CONSIDERED IN CONSTRUCTION?
- COST OF INSTALLATION OF A PREfabricated WAREHOUSE
Today, most manufacturing businesses require a quality infrastructure system of machinery, warehouses, and factories to support and promote the production process. Depending on the nature and characteristics of each type of goods, each business will have its own requirements for warehouse construction. However, the common point that most businesses want when building warehouses is to find quick construction solutions, save time and costs, but still ensure standard quality and long-term durability. and high aesthetics.
One of the optimal solutions favored by many businesses today is to build prefabricated warehouses . This is a perfect choice that fully meets the criteria of construction speed, reasonable cost, and sustainable quality. So, what is a prefabricated warehouse? What are the outstanding features and costs of building this type of warehouse? Let's explore details about our warehouse products with Hoang Sa Viet to learn more about the benefits this solution brings to your business.
WHAT IS A PREfabricated WAREHOUSE? FUNCTION OF STEEL FRAME WAREHOUSE
1. What is a prefabricated warehouse?
Prefabricated warehouses, also known as steel frame warehouses, are becoming a popular and modern construction method in today's construction industry. This is an improved version of the traditional prefabricated house model, bringing many outstanding advantages both technically and aesthetically. In this construction method, the warehouse 's frame is made from stainless steel materials, combined with wall panels using high-quality 3-layer panel material, helping to improve heat insulation, sound insulation, and durability. Durable compared to traditional corrugated iron walls.
SEE MORE PRODUCTS:
The process of building a prefabricated warehouse includes three main stages: design, component processing, and installation at the construction site. The design phase is the first and very important step, ensuring that every detail of the warehouse is carefully calculated to meet usage requirements and optimize functionality. After completing the design, steel components will be processed at the factory with high precision, before being transported to the construction site for assembly.
The highlight of prefabricated warehouses is the extremely quick construction time. Thanks to a closed and standardized assembly process, completing a warehouse can take only a short amount of time, significantly saving labor costs and minimizing negative impacts on the surrounding environment. With these advantages, prefabricated warehouses are not only an ideal choice for businesses that need to expand production scale but are also suitable for projects that require flexibility and resource optimization.
SEE MORE ARTICLES
20 newest Container house models this year
Refer to the 50 most beautiful smart prefabricated house models!
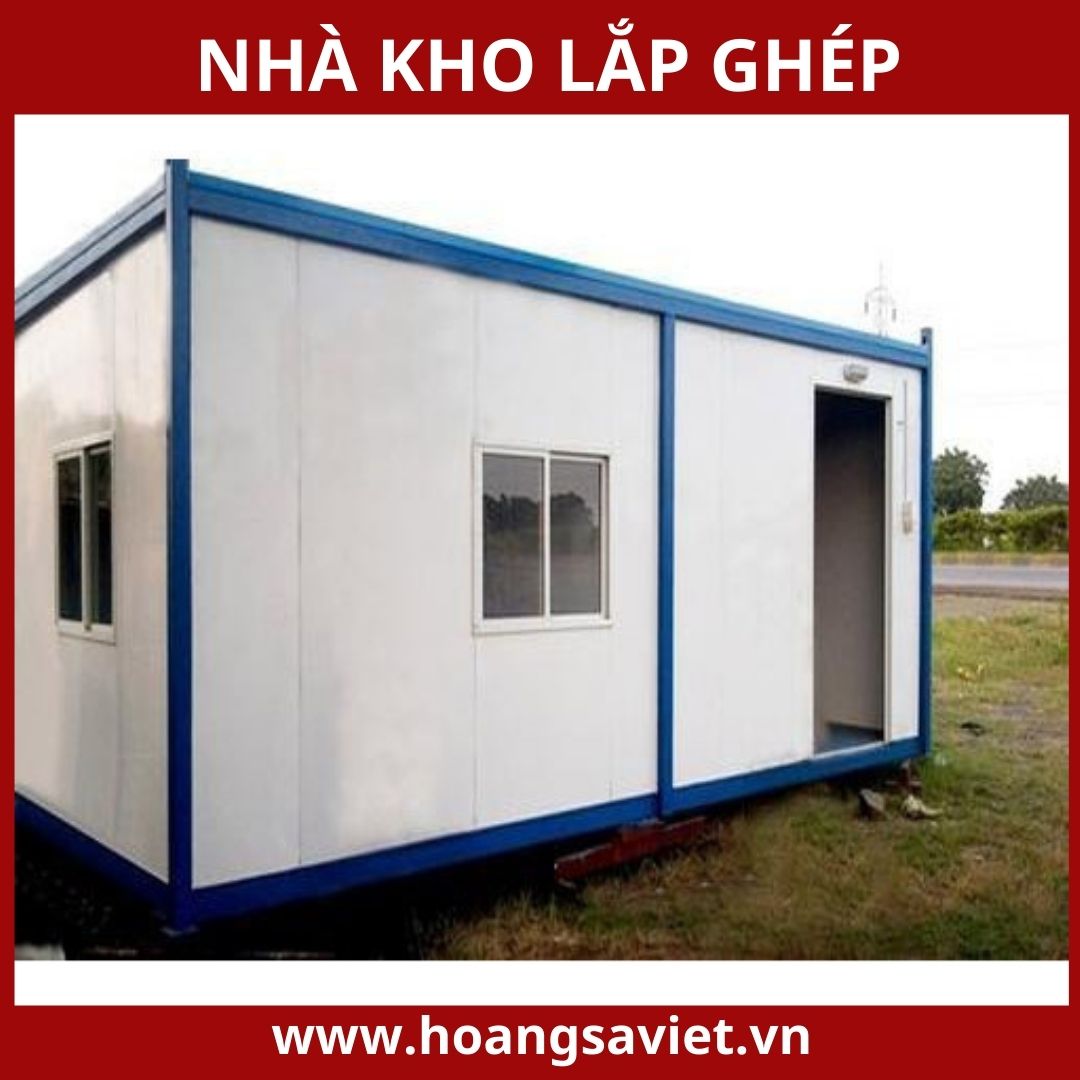
2. Function of prefabricated warehouse
Warehouses play an extremely important role in the operating system of manufacturing enterprises, and its functions do not just stop at storing goods but also cover many other aspects to optimize business activities. So what are the specific functions of the warehouse?
Storing and preserving goods
One of the most important functions of a warehouse is to store and preserve goods. The warehouse is equipped with a sturdy shelving system and a modern power management system, helping businesses store goods safely and scientifically. When owning a quality warehouse , businesses can effectively control the storage process, thereby easily managing the quantity and quality of goods, and minimizing the risk of damage due to environmental conditions. not favorable. This not only protects the business's assets but also enhances their reputation in the eyes of customers and partners.
SEE MORE PRODUCTS:
Coordination of goods
The warehouse is also a goods coordination center, especially useful for businesses with many diverse product lines. Owning a warehouse helps businesses easily classify goods according to each order or specific customer request. Thanks to careful preparation at the warehouse, the sales and delivery process takes place faster and more smoothly. This not only optimizes time but also improves operational efficiency, helping businesses quickly respond to market needs.
Aggregate and distribute goods
In addition to its storage role, warehouses also play an extremely important role in synthesizing and distributing goods, contributing to optimizing the entire supply chain of a business. This is the place where products from many different sources are gathered, helping to consolidate retail shipments into larger volumes. This not only helps businesses easily divide storage areas and manage goods scientifically, but also creates favorable conditions for distributing goods to retail locations or other distribution centers. This consolidation ensures that operations run smoothly and efficiently, minimizing the risk of errors and saving time and costs in transportation.
SEE MORE ARTICLES
20 newest Container house models this year
Refer to the 50 most beautiful smart prefabricated house models!
In general, the warehouse is not simply a storage place but also an indispensable part of the enterprise's logistics system. With the function of synthesizing and distributing goods, warehouses make an important contribution to maintaining a continuous flow of goods, ensuring that products are supplied to the market on time and as required. This is an important factor to help businesses enhance their competitiveness, develop sustainably, and achieve success in an increasingly fierce market.
BASIC STRUCTURE OF A PREfabricated WAREHOUSE
The structure of the warehouse should pay attention to the following structures: ceiling, floor, walls and wall corners, doors, windows, ventilation system, lighting system, water supply and drainage system. The prefabricated warehouse includes basic structural parts such as:
+ Main frame system (columns and trusses).
+ Secondary structural parts (purlins, wall struts and wall beams).
+ Steel panels formed by rolling (roof and wall panels).
.jpg)
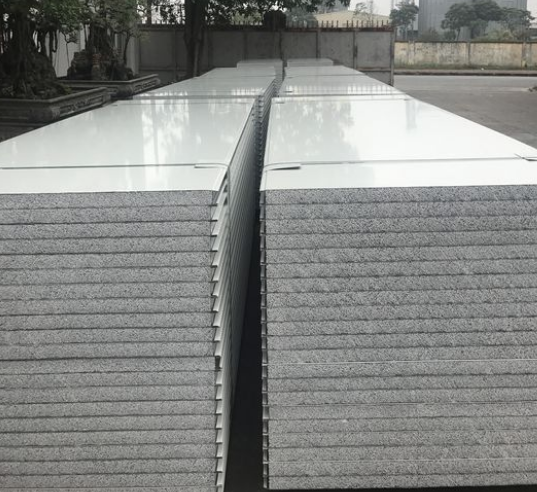
BASIC EQUIPMENT REQUIRED IN THE WAREHOUSE
To achieve the best operating performance, a warehouse needs to be equipped with equipment such as:
+ Warehouse shelves: help increase storage capacity in the same warehouse area, one warehouse area. It is necessary to carefully choose the quality of shelves that are safe to use. There are several types of shelves that are widely used today: medium-duty shelves, selective shelves, double deep shelves, drive-in shelves, support arm shelves, etc.
+ Forklifts: such as electric vehicles, hand trucks, shopping carts, and motorized forklifts, help move goods onto shelves easier and save more time.
+ Pallets for goods: have many sizes, made from wood, plastic, iron materials suitable for each type of goods, helping to preserve goods better.
+ Safety equipment: need to fully install explosion-proof equipment, protective clothing, area signs, etc.
SEE MORE PRODUCTS:
WHY IS THIS THE PRIORITIZED SOLUTION, WHAT ADVANTAGES DOES IT HAVE?
Prefabricated warehouses are increasingly becoming the top choice of businesses thanks to a series of outstanding advantages, meeting the needs of building modern, economical and environmentally friendly warehouses.
1. Use lightweight materials to reduce load pressure:
One of the great advantages of prefabricated warehouses is the use of lightweight materials. This not only helps reduce load pressure on the foundation, but also minimizes construction costs. Furthermore, these materials are often highly recyclable, contributing to environmental protection and limiting pollution. Using these environmentally friendly materials not only helps businesses comply with environmental protection regulations but also enhances brand image and affirms the business's commitment to sustainable development.
2. Suitable for many types of terrain and soil properties:
Prefabricated warehouses can be built on many different types of terrain, from soft soil, loose soil to seismic areas. This is an outstanding advantage that helps this model be flexible in choosing construction locations, suitable for many different natural conditions. The ability to construct on complex grounds while still ensuring stability and safety is a strong point that helps prefabricated warehouses become the ideal solution for businesses wishing to build warehouses. factories in many different geographical regions.
SEE MORE ARTICLES
20 newest Container house models this year
Refer to the 50 most beautiful smart prefabricated house models!
3. High resistance to mold and moisture:
One of the big challenges that businesses face when building warehouses is controlling mold, especially in areas with humid climates. Mold conditions not only directly affect the quality of stored goods but can also cause damage to the warehouse structure, leading to expensive maintenance and repair costs. Understanding this problem, prefabricated warehouses are designed with outstanding mold resistance, using advanced materials and technology to ensure the storage environment is always dry and cool.
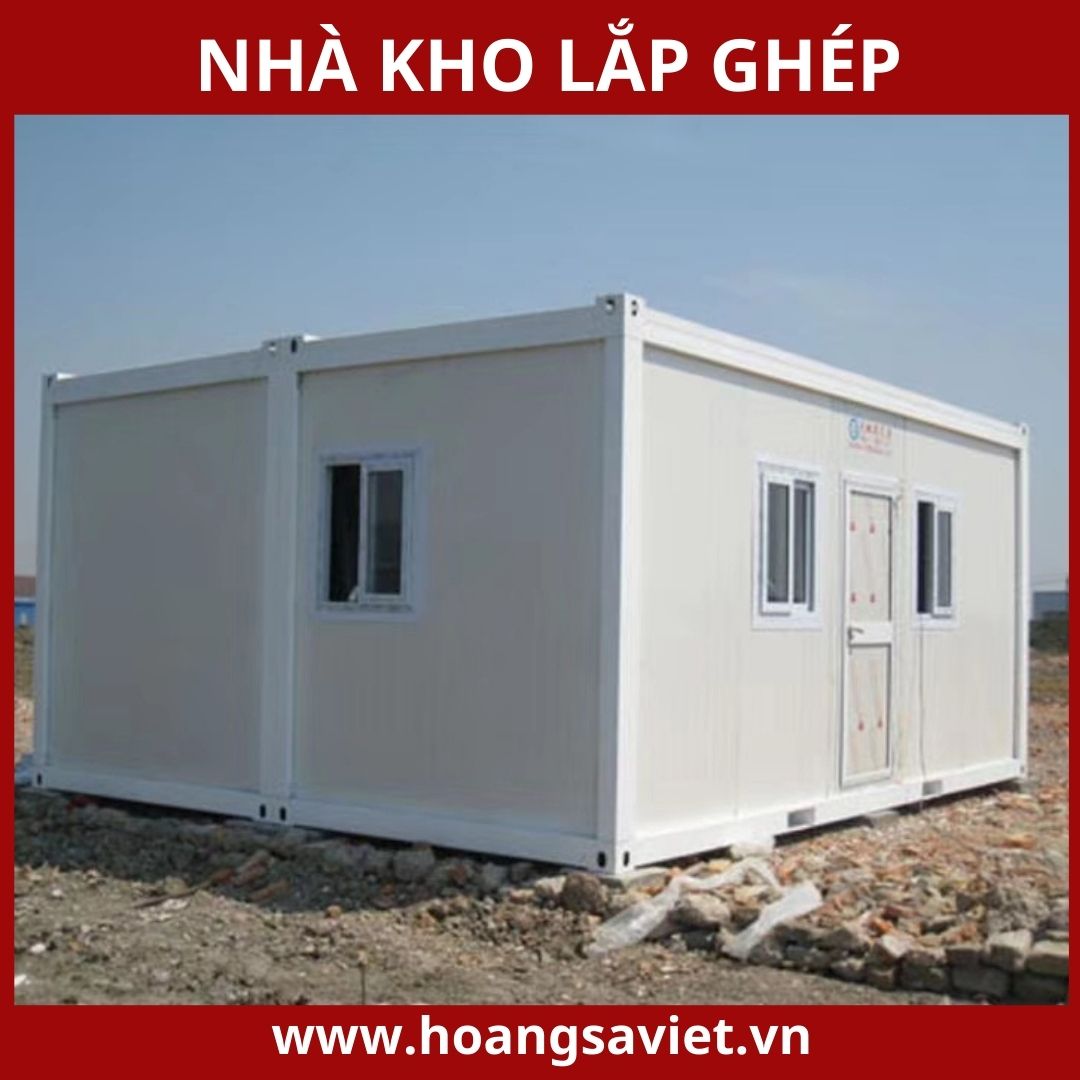
Moisture resistance not only helps protect goods from the negative effects of environmental conditions but also prolongs the lifespan of the warehouse, helping businesses save significantly on maintenance and repair costs throughout the process. usage process. This makes prefabricated warehouses an ideal choice for businesses, especially those operating in harsh climates, where moisture resistance is essential. set. Thanks to that, businesses can rest assured that goods are always preserved in the best conditions, thereby maintaining product quality and improving business efficiency.
4. Quick and effective construction:
The joints and components of the prefabricated warehouse are manufactured and finished at the factory, ensuring every detail is accurate according to technical drawings. Once completed, all these components will be transported to the construction site for assembly. With this production and assembly process, the construction time for prefabricated warehouses is significantly shortened compared to traditional construction methods. Because the components are pre-machined, assembly at the construction site becomes quick, accurate and effective, helping to minimize risks and errors during the construction process. This not only helps businesses quickly put the warehouse into operation, promptly meeting the needs of production and storage of goods, but also contributes to minimizing additional costs such as labor, construction equipment and construction site management. Therefore, the prefabricated warehouse model is becoming the preferred choice of many businesses today, both ensuring construction progress and optimizing construction costs, bringing high economic efficiency. .
SEE MORE PRODUCTS:
5. Save labor and construction costs:
Thanks to the quick assembly process, prefabricated warehouses not only help businesses save significantly on labor and construction costs, but also optimize resources effectively. Short construction time means businesses can minimize costs related to hiring and maintaining workers, while limiting other costs such as operating costs, site management, and machinery maintenance throughout the construction process. This is one of the key factors that helps prefabricated warehouses become an ideal economic solution, especially suitable for businesses looking to optimize investment costs while still ensuring quality. construction and long-term efficiency.
In general, with outstanding material advantages such as recyclability, high flexibility in adapting to many different types of terrain, outstanding resistance to mold and mildew, along with a quick construction process. , cost-effective, prefabricated warehouses are truly a perfect solution for modern businesses. This model not only meets the need for a sustainable and safe warehouse system, but also contributes to creating great economic values, helping businesses maintain and improve production and business efficiency during this period. long time.
SEE MORE ARTICLES
20 newest Container house models this year
Refer to the 50 most beautiful smart prefabricated house models!
CONSTRUCTION PROCESS OF PREfabricated WAREHOUSE
First phase: Construction of the foundation, leveling the ground, digging the foundation...
Stage 2: Install the steel frame, connected together with bolts. Assembling purlins and tie cables creates stability and support for the steel frame.
Phase 3: Construction of walls and partitions.
Phase 4: Construction of infrastructure, including water supply and drainage systems and road systems. This is an important part to maintain operational activities.
Phase 5: Technical systems are installed including fire protection, electrical systems, control and operation cabinets...
Final stage: Complete the remaining parts such as cleaning the warehouse and checking the systems thoroughly to hand over to the owner.
IN WHICH LOCATIONS DO YOU NEED ATTENTION IN WAREHOUSE INSTALLATION FOR CONSTRUCTION?
When installing and building a warehouse, choosing a suitable location is a key factor to ensure effective operation and storage of goods. First of all, warehouses need to be located in locations not affected by polluted environments, away from places prone to water stagnation or flooding, because these factors can cause serious damage. important for goods as well as affecting the warehouse's infrastructure.
In addition, the warehouse location should be chosen to be spacious, airy, and have enough clean water to serve necessary living and operating needs. Convenient location for moving goods, near main traffic routes, is also an important factor, helping the import and export process of goods take place faster and more effectively.
In addition, operating systems inside the warehouse, from power management systems, shelving systems, to waste treatment systems, need to be designed and installed according to strict hygiene standards. strict, ensuring not to pollute the environment. This not only protects the surrounding environment but also contributes to maintaining a safe, clean working environment, ensuring the health of workers and preserving goods well. Therefore, careful consideration of location and standards when building a warehouse not only brings economic efficiency but also demonstrates the business's responsibility towards the environment and society.
SEE MORE PRODUCTS:
COST OF INSTALLATION OF A PREfabricated WAREHOUSE
Installation costs will include the following basic items:
+ Depending on the warehouse construction area, the price will be calculated per 1m2.
+ Materials selected for construction.
+ Consulting fee and warehouse drawing design.
+ According to requirements, install systems: electricity, water, fire protection system, transformer station system...
+ Hire workers.
Modern prefabricated warehouse models, you can refer to
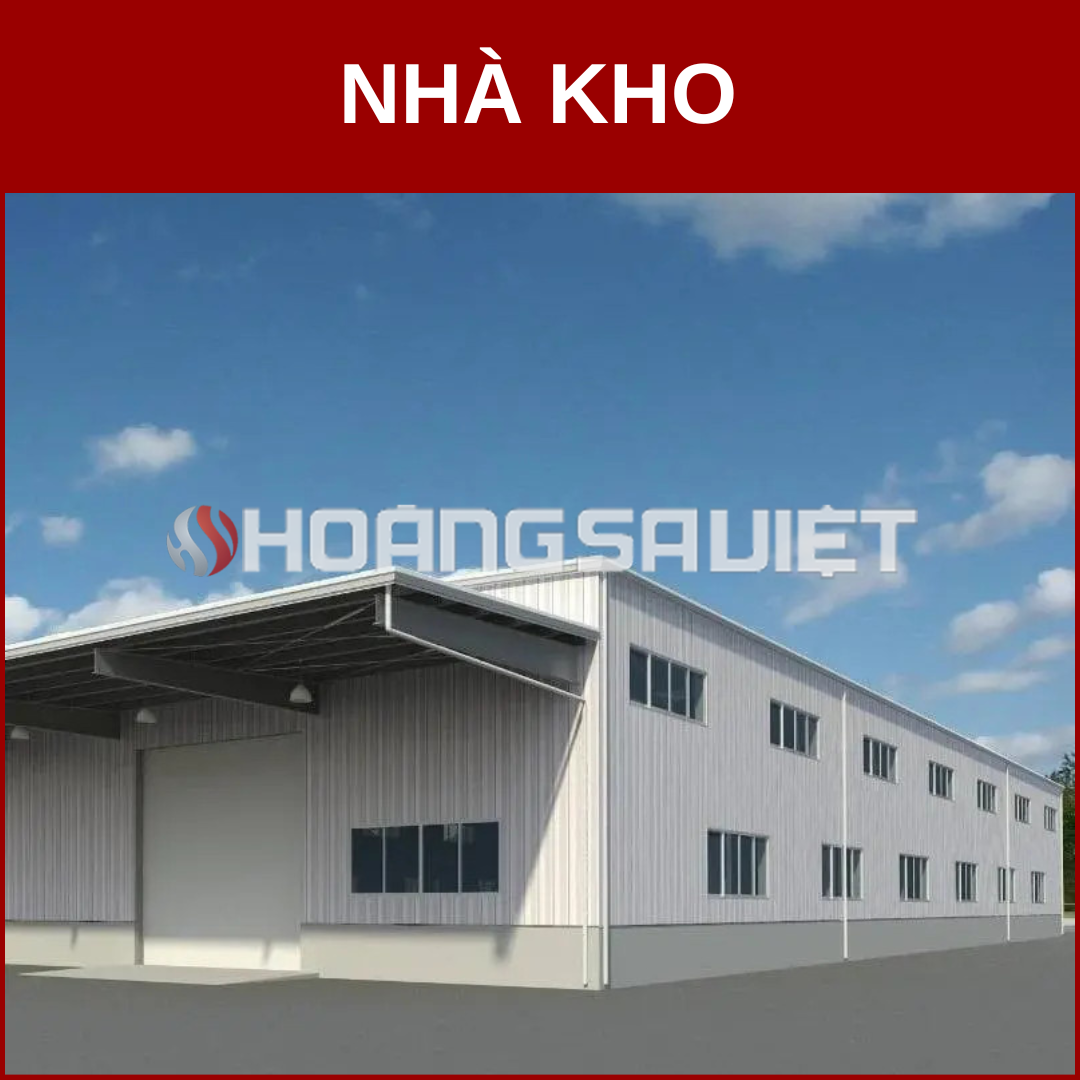
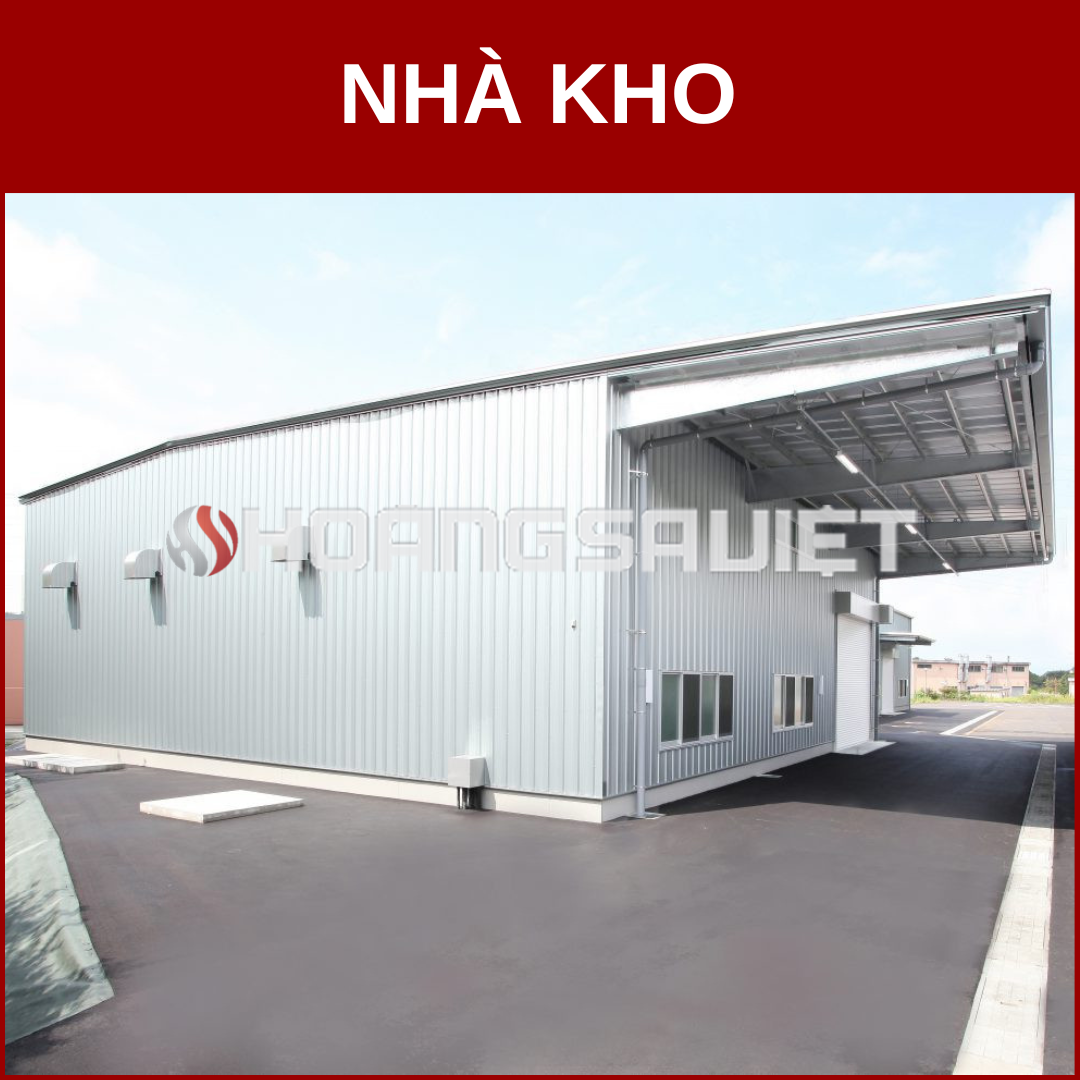
SEE MORE PRODUCTS:
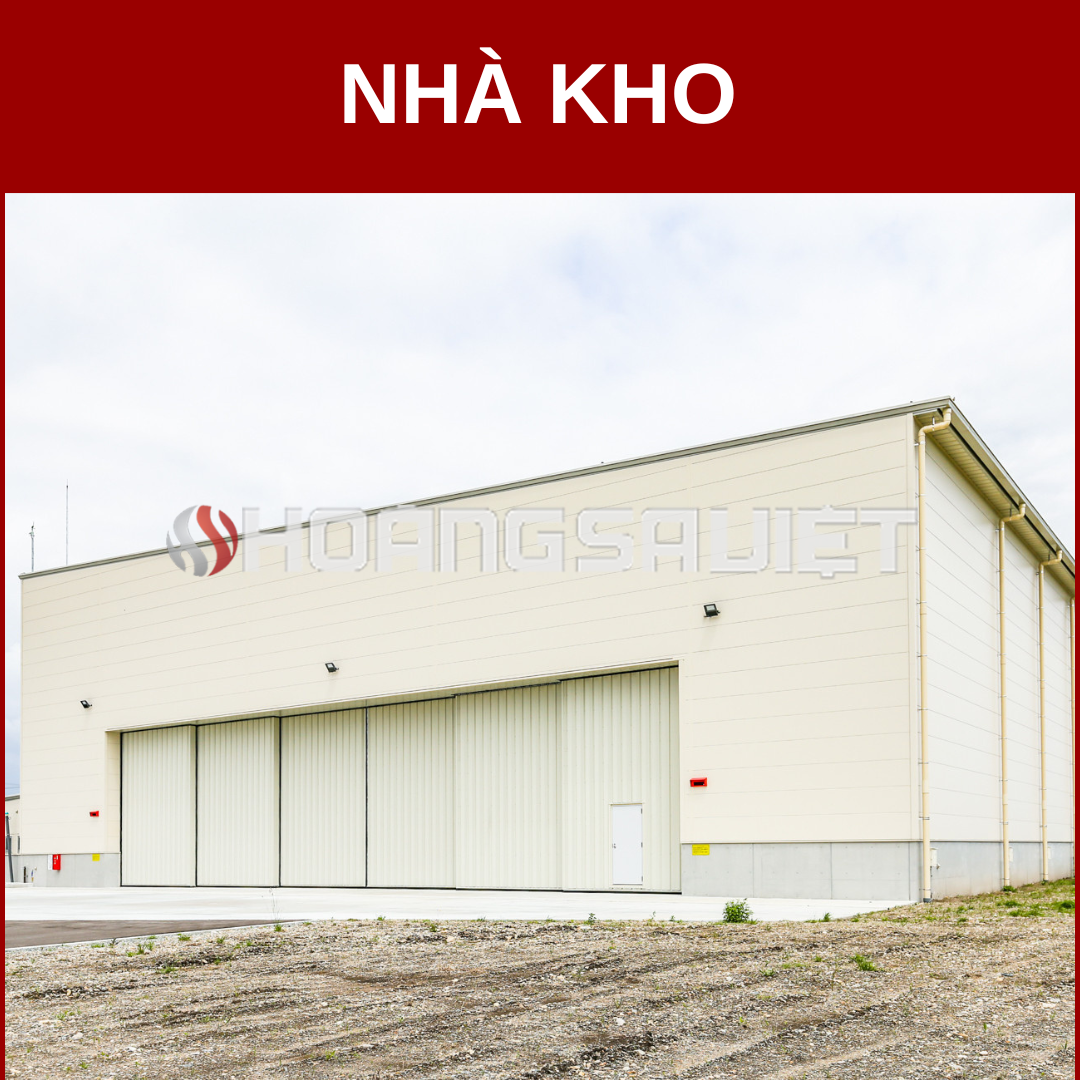
For more advice on the most optimal design solutions for prefabricated warehouses, please contact:
Ms.Linh 0907.090.551 (Business)
Hiện chưa có đánh giá nào về sản phẩm này!