The system is processing. Please wait a moment!
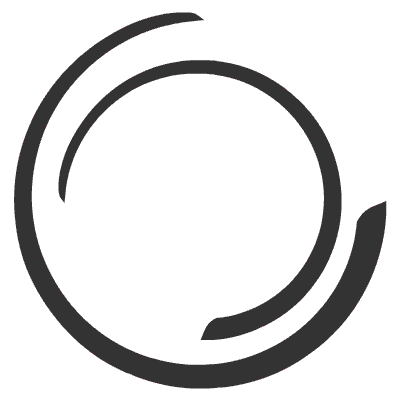
Vui lòng lựa chọn loại báo giá!
- Home Product prefab modular house
Prefabricated Houses for the Global Market
- Unit price: Calculated by m2 (3.5 - 5.5 million/m2)
- Model: Prefabricated Houses for the Global Market
- Brand: Hoang Sa Viet Construction
- Frame material: 2.5mm thick U160mm steel, tempered - electrostatic
- Wall material: 2-layer Rockwool 50mm specialized panel
- Insulation capacity: 95%
- Fire resistance: 100%
- Connection Type: Smart Connector
- Electrical system: Basic (LED lights, sockets, circuit breakers)
- Warranty: 10 Years
TABLE OF CONTENTS
- What Are Modular Homes?
- Understanding Modular Homes.Benefits of Modular Homes
- Benefits of Modular Homes
- Types of Modular Homes for Different Markets
- Case Studies of Successful Modular Home Projects
- Challenges and Solutions in Modular Home Construction
- Expert Opinions on the Future of Modular Housing
- Expanding Business Globally: Exporting Modular Homes
What Are Modular Homes?
In today’s rapidly evolving world, housing affordability and sustainability have become major concerns. As populations grow and urban spaces become more crowded, the need for cost-effective and efficient housing solutions has increased. One of the most promising innovations in modern construction is modular housing—a building method that involves fabricating sections of a home in a factory before assembling them on-site.
Modular homes, also known as prefabricated homes, prefab houses, or factory-built homes, offer a faster, more affordable, and environmentally friendly alternative to traditional home construction. Unlike conventional houses, which are built entirely on-site, modular homes are constructed in sections at an off-site facility. These prefabricated sections are then transported to the final location, where they are assembled and installed on a permanent foundation.
This method is revolutionizing the construction industry by significantly reducing waste, saving time, and lowering overall costs, making modular homes a viable option for various markets, including affordable housing projects, disaster relief housing, and luxury real estate developments.
>>> Detailed price list for complete construction of prefabricated houses under 100 million
.jpg)
The Growing Demand for Prefabricated Houses
The modular home industry is experiencing exponential growth due to several factors:
- Rapid Urbanization: With increasing populations in cities worldwide, there is a high demand for affordable and quickly constructed housing solutions.
- Cost Efficiency: Rising material and labor costs have made traditional home construction less accessible to many people. Prefab homes offer a budget-friendly alternative.
- Sustainability: As environmental concerns grow, energy-efficient and eco-friendly building solutions like modular homes are gaining popularity.
- Technological Advancements: Innovations in smart home technology, energy-efficient materials, and 3D printing have improved the quality and functionality of prefab homes.
>>> Detailed price list for complete construction of prefabricated houses under 200 million
.jpg)
Why Modular Housing is a Game-Changer in Affordable Living
One of the biggest advantages of modular housing is its affordability without compromising quality. For as little as $70,000 to $300,000, people can own a durable and modern home. Governments and private sectors worldwide are investing in modular housing solutions to tackle housing shortages and provide better living conditions for communities in need.
Additionally, modular homes are highly adaptable, making them suitable for various applications such as residential living, offices, temporary shelters, and commercial spaces. Whether it’s a small container home or a fully customized modular villa, this housing innovation is here to stay.
SEE MORE ARTICLES
20 Latest Container House Models This Year
Check out the 50 most beautiful smart prefabricated house models!
SEE MORE PRODUCTS:
Understanding Modular Homes
Definition and Features
A modular home is a prefabricated structure built in a controlled factory environment before being transported to its final destination for assembly. Unlike mobile homes, modular homes are permanent structures that comply with the same local building codes as traditional houses.
Key Features of Modular Homes
Factory-Built Construction – Built in sections at a manufacturing facility.
High-Quality Materials – Uses durable materials like steel frames, insulated panels, and energy-efficient roofing.
Customizable Design – Homeowners can choose layouts, finishes, and add-ons.
Sustainable and Energy-Efficient – Reduced construction waste and better insulation.
Quick Assembly – Can be completed in weeks instead of months compared to traditional construction.
Key Components of Modular Construction
Modular homes consist of several prefabricated modules that are built separately and later connected at the site. These components include:
- Steel or Wooden Frame: Provides the structure and support.
- Insulated Wall Panels (Panelized System): Made from concrete, SIPs (Structural Insulated Panels), or lightweight steel.
- Flooring and Roofing: Designed to be energy-efficient and weather-resistant.
- Electrical and Plumbing Systems: Pre-installed in the factory, reducing on-site labor time.
Benefits of Modular Homes
Cost-Effective Solution
One of the primary reasons why modular homes are becoming more popular is their affordable pricing. Because they are manufactured in a factory setting, costs related to on-site construction—such as labor, material waste, and weather delays—are significantly reduced.
Fast Construction Time
Traditional homes take 6-12 months to build, whereas modular homes can be ready in just 4-8 weeks. The majority of work happens off-site, allowing parallel construction of both the foundation and the housing structure.
Eco-Friendly and Sustainable
Modular homes are built with sustainability in mind:
- Less Waste – Factory production allows for precise material usage.
- Energy Efficiency – Many prefab homes use solar panels, insulation materials, and LED lighting to reduce energy consumption.
- Recyclable Materials – Many modular homes use reclaimed wood, metal, and composite materials that are eco-friendly.
Customizable Designs
Unlike mobile homes, modular homes allow for endless customization. Homeowners can choose:
- Floor plans and layouts (studio, single-story, two-story).
- Interior and exterior finishes (wood, metal, glass, concrete).
- Smart home integrations (automated lighting, energy-efficient systems).
Durability and Strength
Modular homes are engineered to be structurally strong, capable of withstanding earthquakes, hurricanes, and extreme temperatures. Many modular homes in the U.S. and Europe are built to exceed traditional building codes.
.jpg)
SEE MORE ARTICLES
20 Latest Container House Models This Year
Check out the 50 most beautiful smart prefabricated house models!
>>> Detailed price list for complete construction of 5x12 prefabricated houses
.jpg)
Types of Modular Homes for Different Markets
Affordable Modular Homes for Low-Income Families
- Budget-friendly, compact designs
- Often used in social housing projects
Luxury Modular Homes: Combining Elegance and Efficiency
- Modern and sleek architecture
- High-end finishes, smart home features
Prefabricated Housing for Disaster Relief and Emergency Situations
- Quick deployment during crises
- Portable and temporary housing solutions
Prefab Homes for Export: Meeting International Housing Needs
- Designed for global markets
- Compliance with regional construction laws and climate conditions
SEE MORE ARTICLES
20 Latest Container House Models This Year
Check out the 50 most beautiful smart prefabricated house models!
Case Studies of Successful Modular Home Projects
Affordable Housing in the United States
In the U.S., modular homes have gained popularity as an affordable housing solution. A prime example is the Austin Affordable Housing Initiative, where modular construction reduced costs by 30% compared to traditional builds. Prefabricated units were assembled in a factory and transported to the site, cutting down construction time from a year to just six months. The use of steel frame modular units ensured durability, while solar panels and efficient insulation reduced energy costs for homeowners.
>>> Detailed price list for construction of 2-bedroom prefabricated house
.jpg)
SEE MORE ARTICLES
20 Latest Container House Models This Year
Check out the 50 most beautiful smart prefabricated house models!
SEE MORE PRODUCTS:
Eco-Friendly Modular Homes in Scandinavia
Scandinavian countries, known for their sustainable architecture, have adopted modular homes to meet their high environmental standards. In Sweden, the Green Living Project built 50 modular eco-homes using recycled materials and triple-glazed windows to improve insulation. These homes were designed to withstand extreme cold while maintaining energy efficiency. The project showcased how modular homes could integrate with smart home technology, including automated heating and cooling systems.
Emergency Housing in Japan
Following natural disasters like earthquakes and tsunamis, Japan has turned to modular housing for rapid reconstruction. In the aftermath of the 2011 Tōhoku earthquake, thousands of modular units were deployed within weeks to provide shelter for displaced residents. Unlike traditional housing, which would take months or even years to rebuild, modular homes offered an immediate and comfortable solution for affected families.
Luxury Modular Homes in Australia
Modular construction is not just for affordability—it’s also making waves in luxury real estate. In Sydney, a project named "The Cliffside Retreat" used modular homes to create high-end, energy-efficient villas. With floor-to-ceiling glass walls, rooftop gardens, and open-concept designs, these homes demonstrated that modular construction can offer luxury features while still being cost-effective and sustainable.
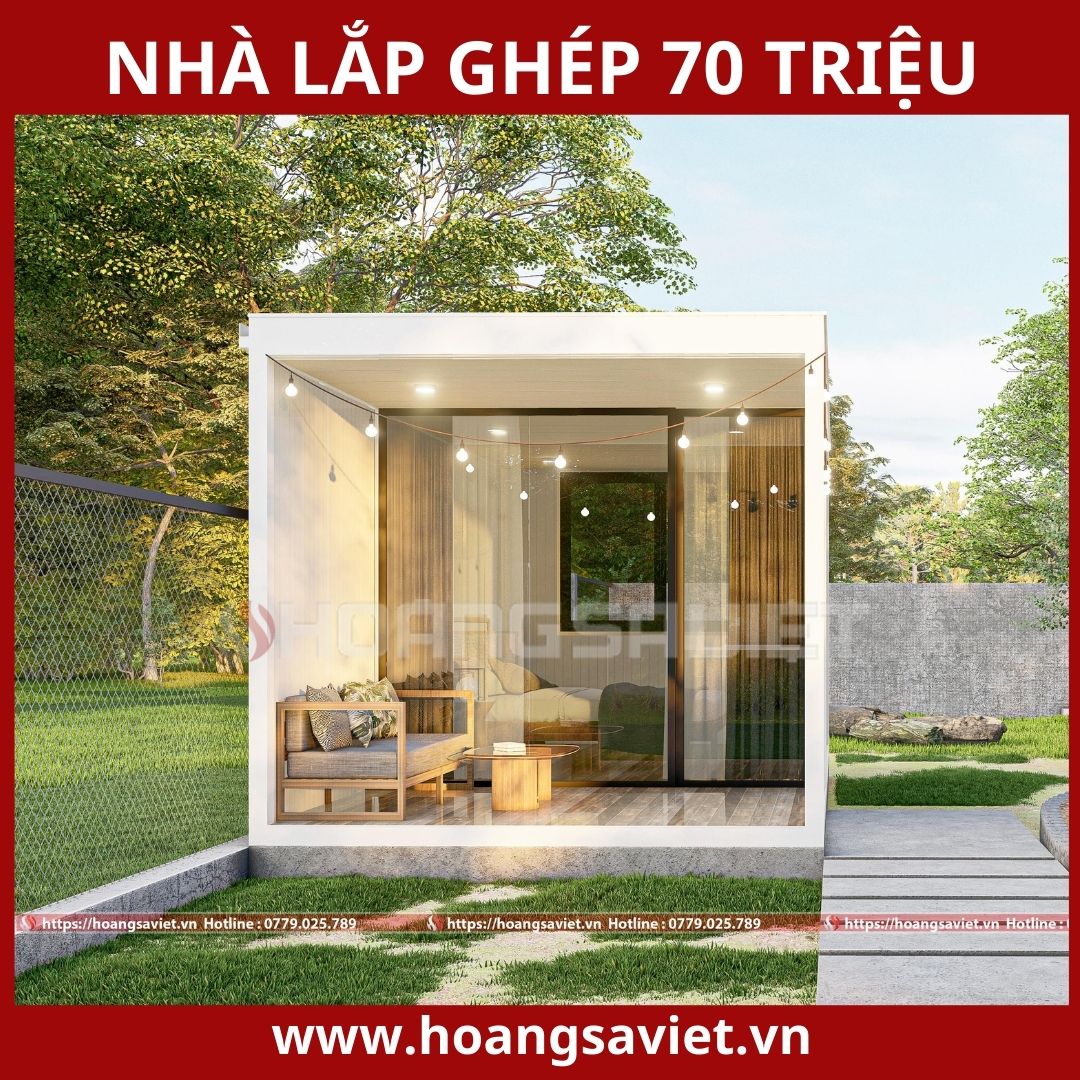
.jpg)
>>> Price list for complete construction of prefabricated container houses from 50 million details
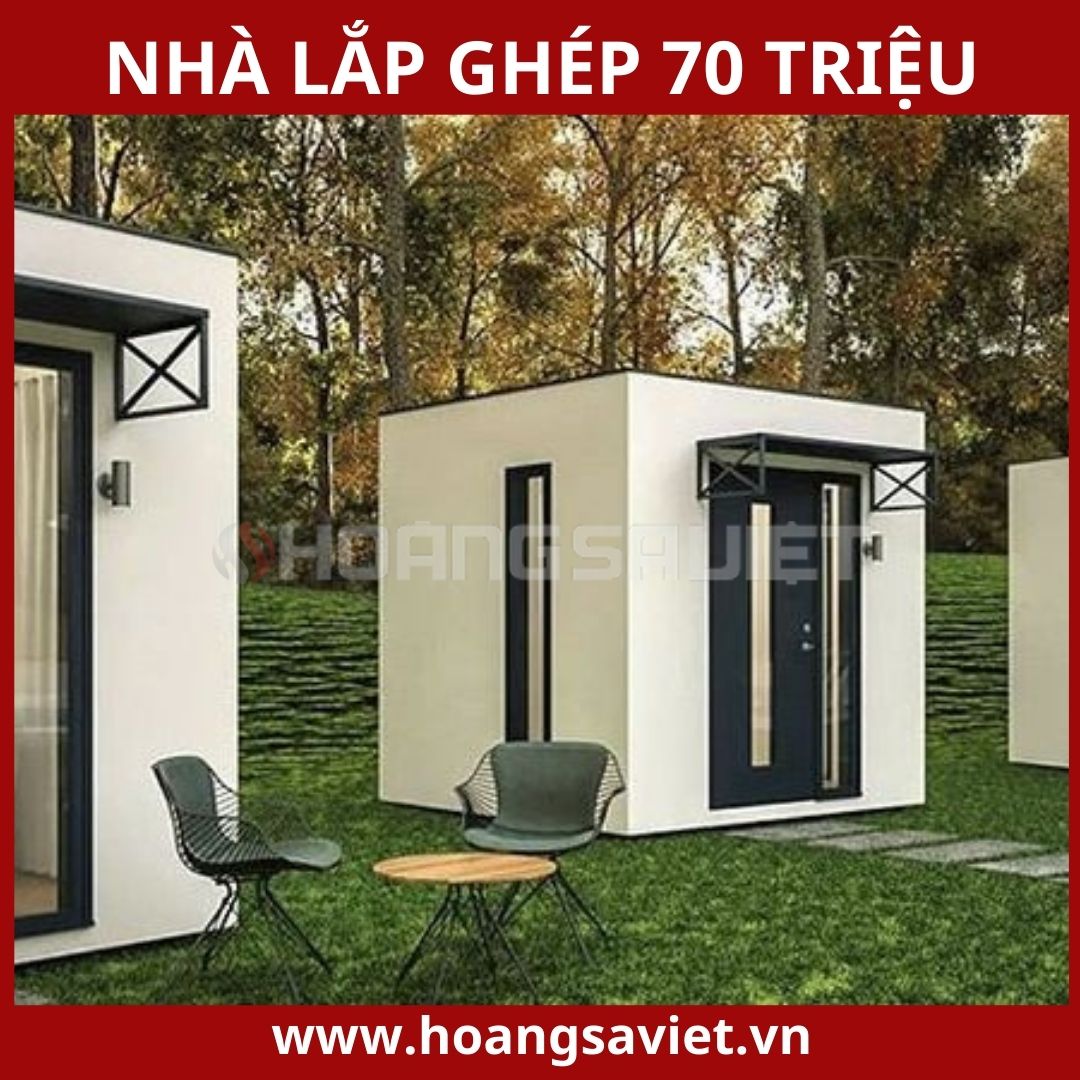
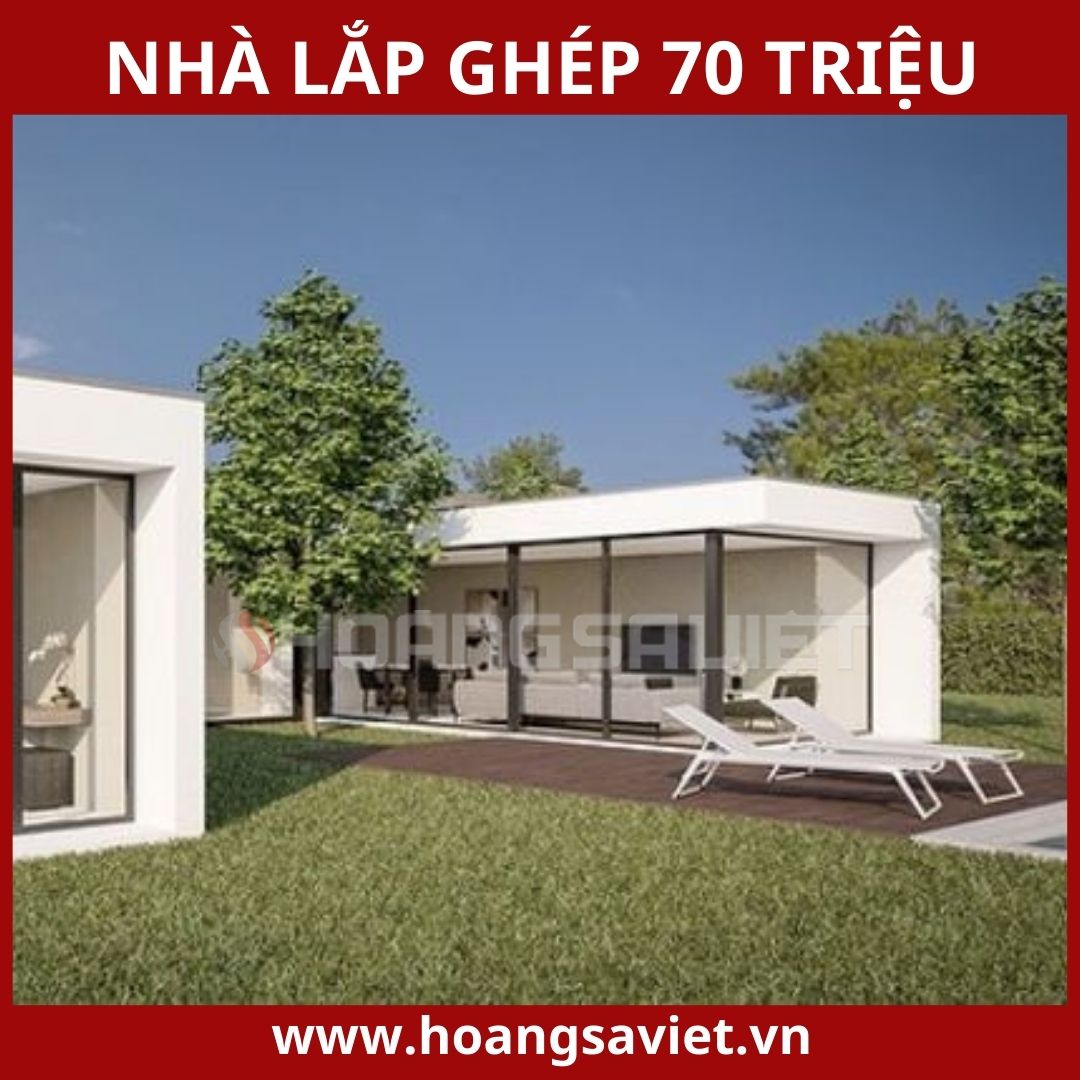
>>> Detailed price list for construction of prefabricated houses from 50 million with Thai roof style
.jpg)
.jpg)
>>> Detailed price list for construction of complete prefabricated houses from 50 million in rural style
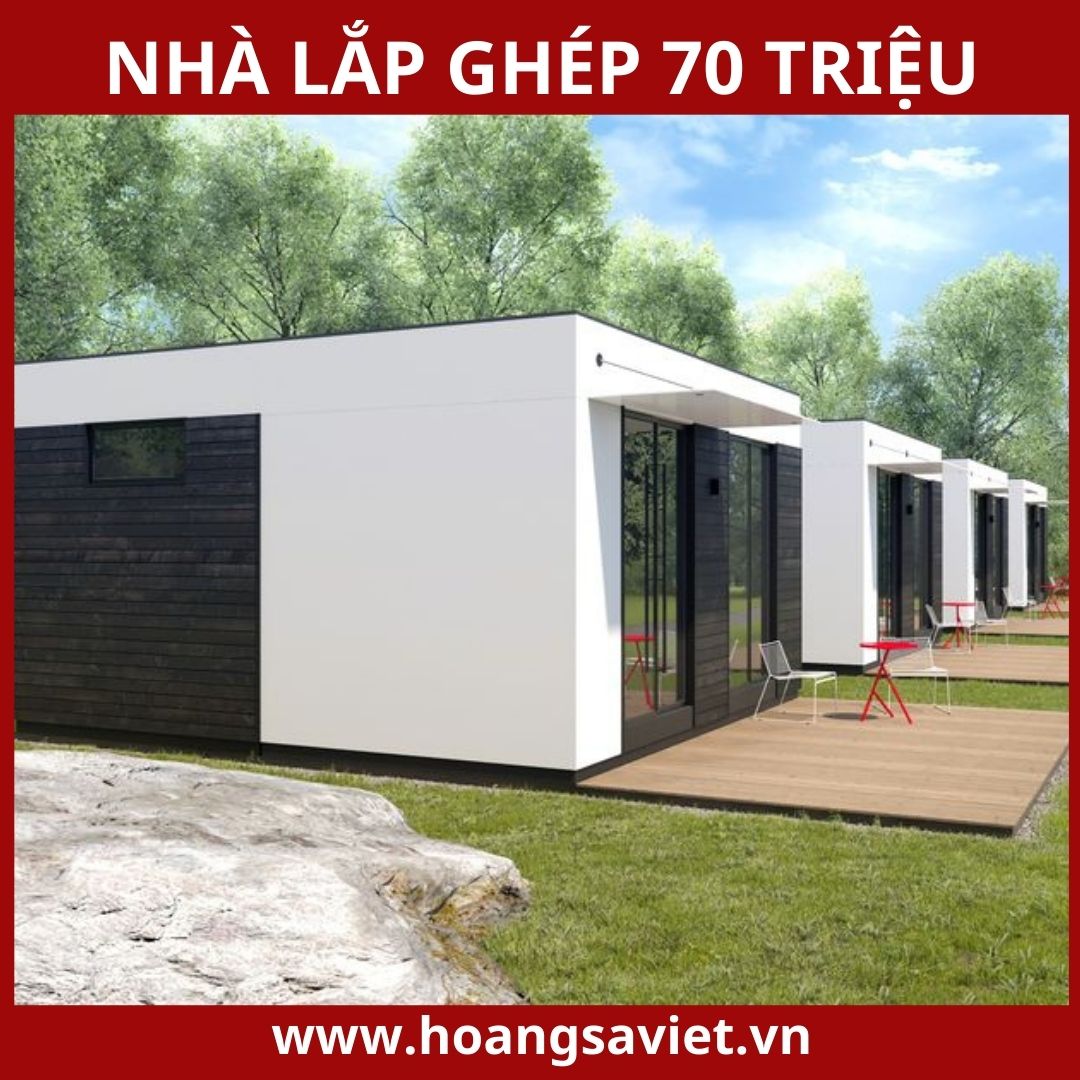
>>> Detailed price list for construction of a 60 million VND prefabricated house in a modern style
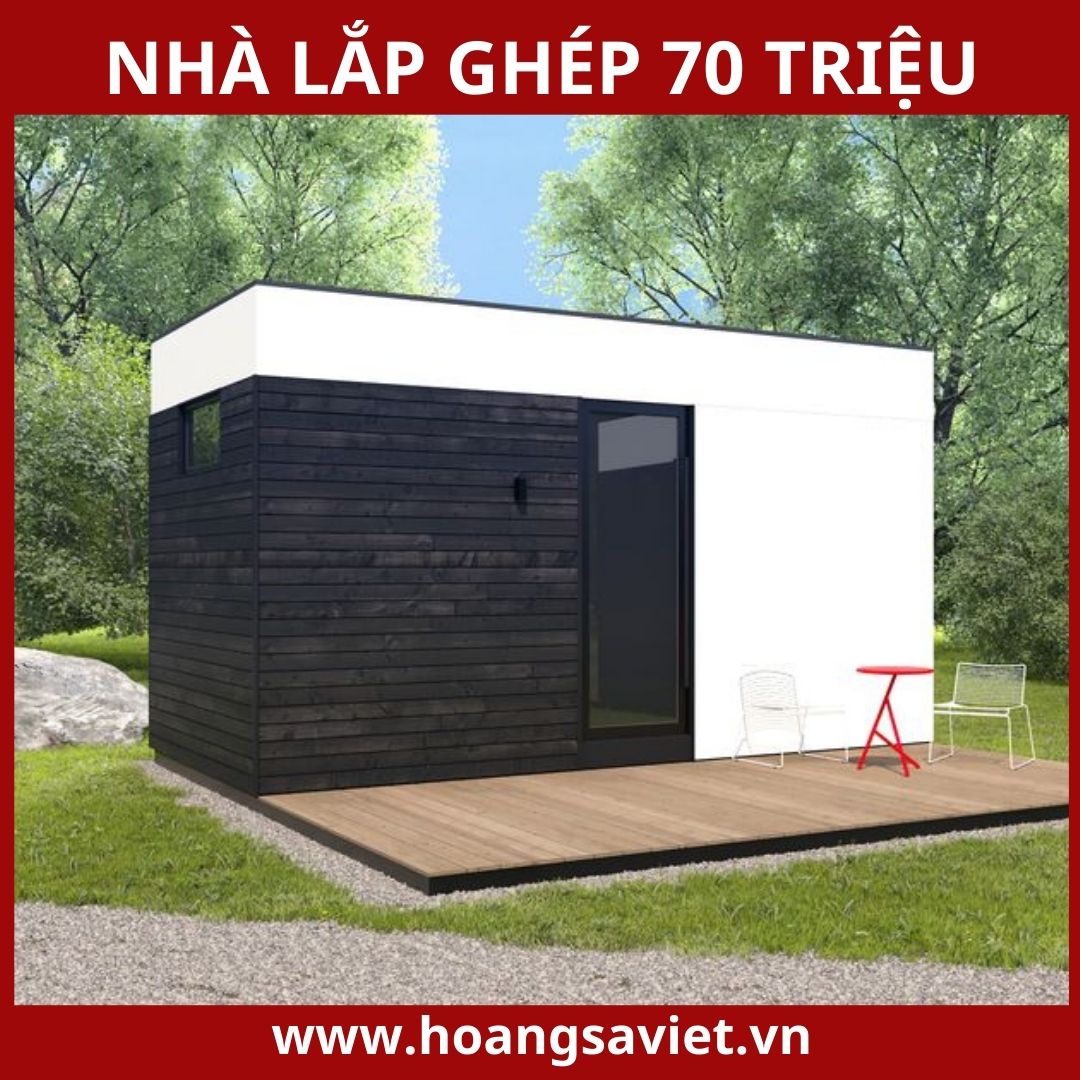
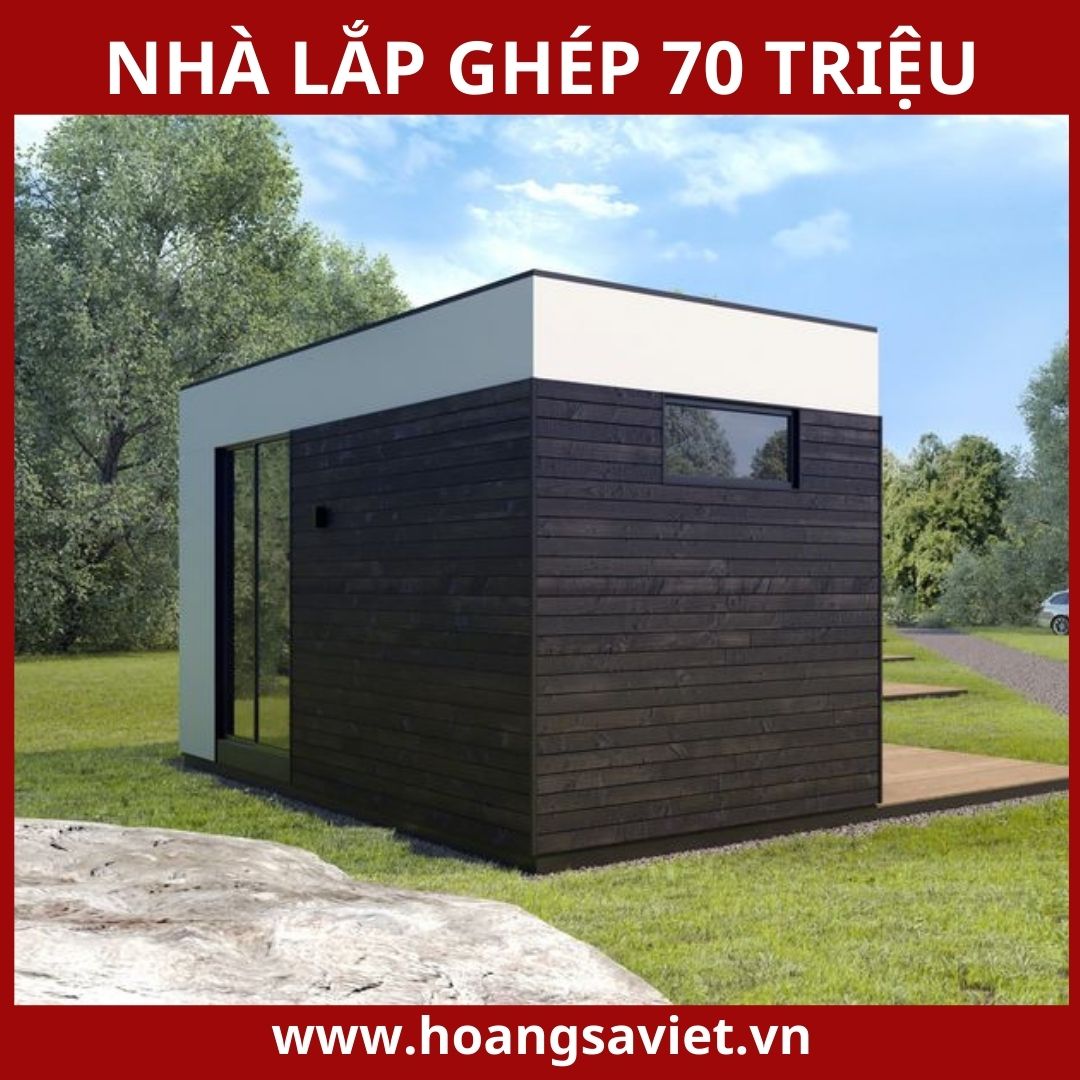
Challenges and Solutions in Modular Home Construction
Permit and Zoning Issues
One of the biggest challenges in modular housing is zoning laws and building permits. Some regions have outdated regulations that do not classify modular homes as permanent structures.
Solution:
- Working with local authorities and lobbying for updated housing policies.
- Partnering with modular home associations to standardize building codes.
- Pre-certifying modular home designs to streamline the approval process.
Transportation and Logistics
Transporting prefabricated sections requires specialized trucks and careful route planning. Some areas have road width restrictions or bridge weight limits that complicate deliveries.
Solution:
- Using collapsible modular units that can be transported efficiently.
- Establishing regional manufacturing hubs to minimize transportation distances.
Customization vs. Standardization
Buyers often worry that modular homes lack customization. While factory-built homes offer cost savings, some fear they might all look the same.
Solution:
- Offering modular design flexibility, where buyers can choose layouts, finishes, and materials.
- Implementing "mix-and-match" modules for personalized floor plans.
Financing Challenges
Traditional banks may hesitate to offer loans for modular homes due to unfamiliarity with the industry.
Solution:
- Partnering with financial institutions to create specialized mortgage programs for modular homes.
- Providing data on modular home resale values to improve bank confidence.
>>> Detailed price list for the construction of a 90 million VND box-shaped prefabricated house
Expert Opinions on the Future of Modular Housing
Growth in Urban Areas
Architect James Peterson, a modular housing expert, predicts that urban modular developments will become the norm. With rising land costs, cities will rely on stackable modular units to create high-density housing.
Green Construction Movement
Sustainability consultant Dr. Laura Chang notes that modular construction will drive eco-friendly building innovations. The reduction in construction waste and energy-efficient designs makes modular homes a key player in the fight against climate change.
AI and Robotics in Prefabrication
Construction engineer Michael Roberts believes automation and AI-driven design will transform modular housing. Future factories will use robotic arms to assemble homes with millimeter precision, cutting labor costs significantly.
Sustainability and Environmental Impact
1. Reducing Construction Waste
Traditional construction generates an estimated 30% of all landfill waste worldwide. Modular homes reduce this by up to 80% through precise material usage and recycling strategies.
2. Energy Efficiency
Modular homes are designed with high-performance insulation, energy-efficient windows, and solar panel integration. A study by the U.S. Green Building Council found that modular homes can reduce energy costs by 40% compared to conventional homes.
3. Eco-Friendly Materials
- Bamboo and engineered wood instead of traditional timber.
- Recycled steel for structural frames.
- Low-VOC paints and adhesives for better indoor air quality.
Comparing Modular Homes to Traditional Construction
Feature |
Modular Homes |
Traditional Homes |
Construction Time |
2-4 months |
8-12 months |
Cost Savings |
10-30% cheaper |
More expensive |
Customization |
High (pre-planned) |
High (on-site) |
Sustainability |
Eco-friendly materials |
Higher waste |
Weather Dependence |
Minimal delays |
Weather delays common |
Expanding Business Globally: Exporting Modular Homes
1. Identifying Target Markets
Countries with housing shortages, disaster-prone areas, and eco-conscious policies present huge opportunities.
>>> Detailed price list for the construction of a 70 million VND prefabricated house, townhouse style
1. Identifying Target Markets
Countries with housing shortages, disaster-prone areas, and eco-conscious policies present huge opportunities.
Key Markets for Modular Home Exports:
- United States: Demand for affordable housing is rising.
- Germany & Scandinavia: Strong sustainability focus.
- Japan: High demand for disaster-resistant homes.
- United Arab Emirates: Interest in luxury modular villas.
2. Overcoming Export Barriers
- Certifications: Meeting EU, US, and Asian building standards.
- Shipping Logistics: Using flat-pack modular units to reduce costs.
- Local Partnerships: Working with construction firms in each country.
Hiện chưa có đánh giá nào về sản phẩm này!