The system is processing. Please wait a moment!
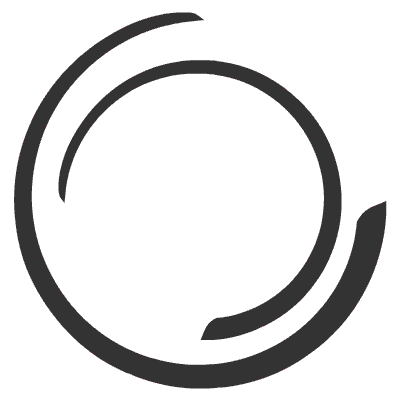
Vui lòng lựa chọn loại báo giá!
- Home Product prefab modular house
2-storey prefabricated house 200 million VND
Code: Nhà Lắp Ghép 2 Tầng
- Model: 2-storey prefabricated house from 200 million
- Unit price: From 3.5 million/m2 of optional area
- Price 200 million , you can build a house from 48-60m2 (each floor is about 24-30m2)
- Option: Toilets, Wooden Floors, Decoration, Decor on request
- Shipping & Assembly: Calculated according to reality
- Brand: Hoang Sa Viet Construction
- Size: 36m2, 48m2, 64m2, 72m2...(1-2 bedrooms)
- Frame material: U160mm steel, 2.5mm thick, tempered - electrostatic
- Wall material: 2-layer specialized 50mm Panel
- Insulation ability: 95%
- Fire resistance: 100%
- Connection type: Smart Connector
- Electrical system included: Basic (LED lights, sockets, CB)
- Warranty: 20 Years
TABLE OF CONTENTS
- WHAT IS A 2-STORY PRESET HOUSE PRICED AT 200 MILLION?
- STRUCTURE OF A 2-STORY Prefabricated House Priced at 200 MILLION
- ADVANTAGES OF PREfabricated HOUSES COMPARED TO TRADITIONAL CONSTRUCTION HOUSES
- HOW IS THE PRICE OF A 200 MILLION 2-STORY ASSEMBLY HOUSE CALCULATED?
- DO I NEED A PERMISSION TO BUILD A 2-STORY ASSEMBLY HOUSE FOR 200 MILLION?
- REFER TO CHEAP 2-STORY ASSEMBLY HOUSE MODELS
For families in towns or cities, where there is a dense population, owning a large plot of land is very difficult, especially for middle-income households. Therefore, with a small land area and limited budget, a 2-storey prefabricated house with a cost of 200 million VND becomes the most optimal solution. In addition, legal issues about land and construction permits also frustrate many people, making construction complicated and time-consuming.
With a plot of land with an average area and an average income, finding a solution to build a house that is aesthetically beautiful and still ensures full functionality for the family is a challenge. With a cost of 200 million VND, you can build a 2-storey prefab house with an area of 48-60m² (each floor is about 24-30m²). This is the perfect choice for families who want a comfortable and convenient living space without investing too much money.
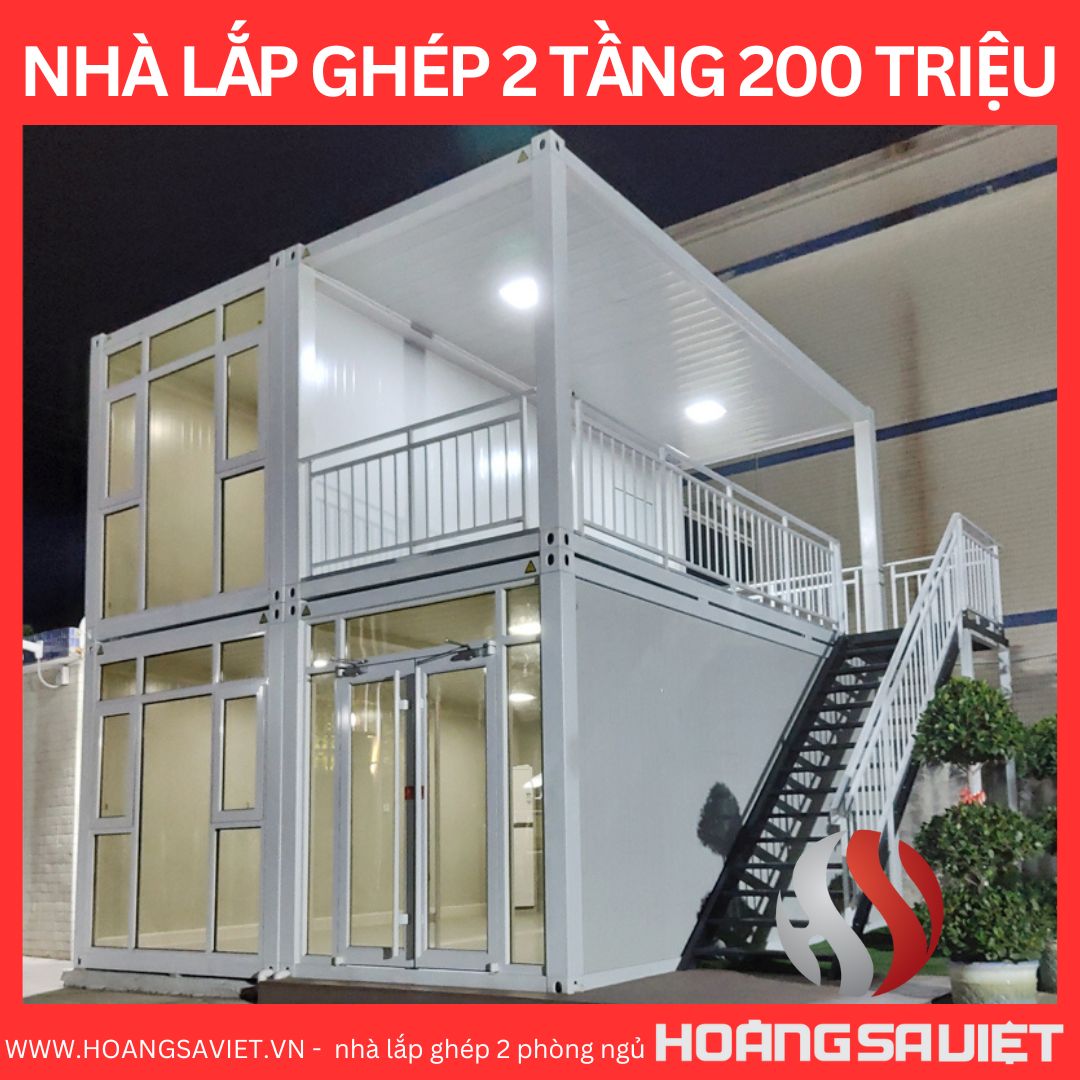
A 2-storey prefabricated house with a cost of 200 million VND not only brings savings in construction costs but also reduces construction time, helping the family quickly have a new place to live. These prefabricated houses are designed with a sturdy structure, using high quality materials, ensuring durability and safety for users. Furthermore, prefabricated houses have flexible customization capabilities, allowing families to change the design and layout of space according to personal needs and preferences.
With an area of each floor from 24-30m², the 2-storey prefab house provides a comfortable and versatile living space. The ground floor can be designed as a living room, kitchen and dining room, creating a common living space for the whole family. The upper floor can accommodate bedrooms and bathrooms, ensuring private and comfortable space for each family member. Flexibility in design allows families to optimize space usage, creating a modern and comfortable living environment.
See more products of Hoang Sa Viet:
If you still do not have a suitable plan for your house project, Hoang Sa Viet Construction will be a reliable choice. With experience and expertise in the field of prefabricated house construction, we will give you detailed suggestions and advice, helping you have a more general overview of this solution. We are committed to bringing you a beautiful, quality, 2-storey prefab house suitable for your budget of 200 million VND.
Let Hoang Sa Viet Construction help you turn your dream of owning a beautiful and comfortable home into reality. We are always ready to accompany you in every step, from design, construction to completion, ensuring you will be satisfied with your choice.
WHAT IS A 2-STORY PRESET HOUSE PRICED AT 200 MILLION?
2-storey prefabricated houses are now becoming quite popular in many countries around the world such as the US, Korea, and Japan, thanks to its outstanding advantages. The 2-storey prefabricated house has a steel frame structure with bearing capacity equivalent to reinforced concrete like a traditional 2-storey house, but with a mass production process using specialized materials, their cost is much cheaper and the time is shorter. Construction time is also significantly shortened.
2-storey prefabricated houses , also known as prefabricated houses, light material houses, or prefabricated steel houses, are designed with high durability and solidity, diverse colors and high aesthetics, but the price is high. extremely reasonable. The main goal of prefabricated houses is to maximize construction costs while still ensuring requirements for rigidity, safety and good insulation. Therefore, prefabricated houses are suitable for all types of projects and are being widely applied in many different fields.
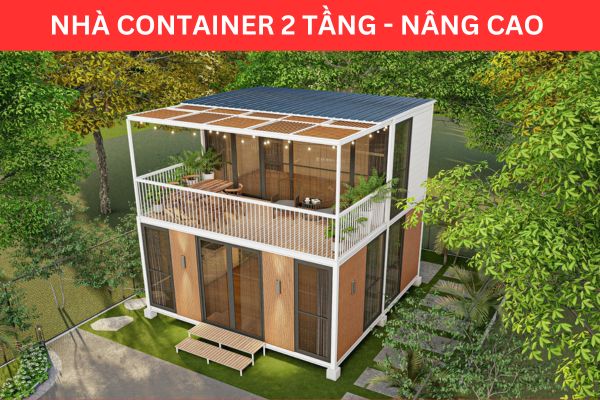
2-storey prefabricated houses are not only used as civil housing but are also very popular in the construction of construction site management houses, housing for workers, factories, motels, resort villas, warehouses, etc. clean rooms - cold storage, supermarkets, clinics, restaurants and even level 4 houses. Prefabricated house modules are pre-manufactured at the factory, then transported to the construction site and assembled quickly, reducing costs. Minimize construction time and costs. This is especially useful in the current context, when the demand for housing and auxiliary works is increasing, while construction costs and construction time are concerns. .
SEE MORE PRODUCTS:
2-storey prefabricated houses also bring great environmental benefits. With the use of recycled materials and a construction process that does not cause much waste, this type of house is more environmentally friendly than traditional construction methods. The good insulation of prefabricated houses also helps save energy, reduce air conditioning costs and create a more comfortable living environment for residents.
The flexibility in design and versatility of 2-storey prefabricated houses have made it the top choice for many modern construction projects. Whether you need a small house for your family or a high-end resort villa, prefabricated houses can meet your requirements. With reasonable prices, quick construction time and guaranteed quality, 2-storey prefabricated houses will definitely be a construction trend in the future.
If you are looking for an effective, economical and environmentally friendly construction solution, a 2-storey prefab house is an option not to be missed. Let Hoang Sa Viet Construction advise and build your dream house with a reasonable budget, providing an ideal and comfortable living space. We are committed to bringing you a quality product that meets all your needs and expectations.
See more products of Hoang Sa Viet:
STRUCTURE OF A 2-STORY Prefabricated House Priced at 200 MILLION
Panel prefabricated houses in house construction are a technology from the Soviet Union and some Eastern European socialist countries. Industrial Panel houses are made up of panels joined together and are widely used.
- The frame is U-shaped, 160mm wide and 2.5mm thick
- Standard panel wall panels for high-rise building construction (glasswool layer in the middle) thickness 50mm
- The floor uses 18mm thick water-resistant CemBoard panels that can withstand heavy loads
- 2-layer heat-resistant roof made of 50mm thick Rockwool glass
- White corrugated aluminum flat ceiling powder coated (4mm thick tone)
- One door and two windows made of aluminum + plastic with dimensions W920*H120mm
- Equipped with basic electrical system including: LED bulbs, CB, electrical socket, wiring and electrical braces
- The foundation is poured with 2 layers of concrete along with iron for fixation
- The area of the 2-storey prefabricated house depending on the customer's choice is usually: 36m2, 48m2, 64m2, 72m2... 1 bedroom, 2 bedrooms, 3 bedrooms, balcony and terrace...
.jpg)
The modern 2-storey prefabricated house is an innovative construction solution, made up of insulated, fireproof panel walls and firmly fixed iron beam frames. These materials not only help the house have good insulation and fire resistance, but also make installation and moving easy and flexible. The size and style of the 2-storey prefabricated house can also be customized according to each customer's needs, providing optimal diversity and convenience.
SEE MORE PRODUCTS:
In order to meet customers' increasing needs for more spacious and comfortable living space, Hoang Sa Viet Construction provides 2-storey prefabricated house models, in addition to conventional level 4 prefabricated house models. Our products ensure sturdiness and outstanding quality, suitable for prefabricated house projects with 2 floors or more. The foundation of the assembled house is poured with solid concrete, combined with firmly reinforced iron beams. Surrounding the house are strong load-bearing columns, while the ceiling uses heat-resistant foam corrugated iron, bringing comfort and sustainability to the living space.
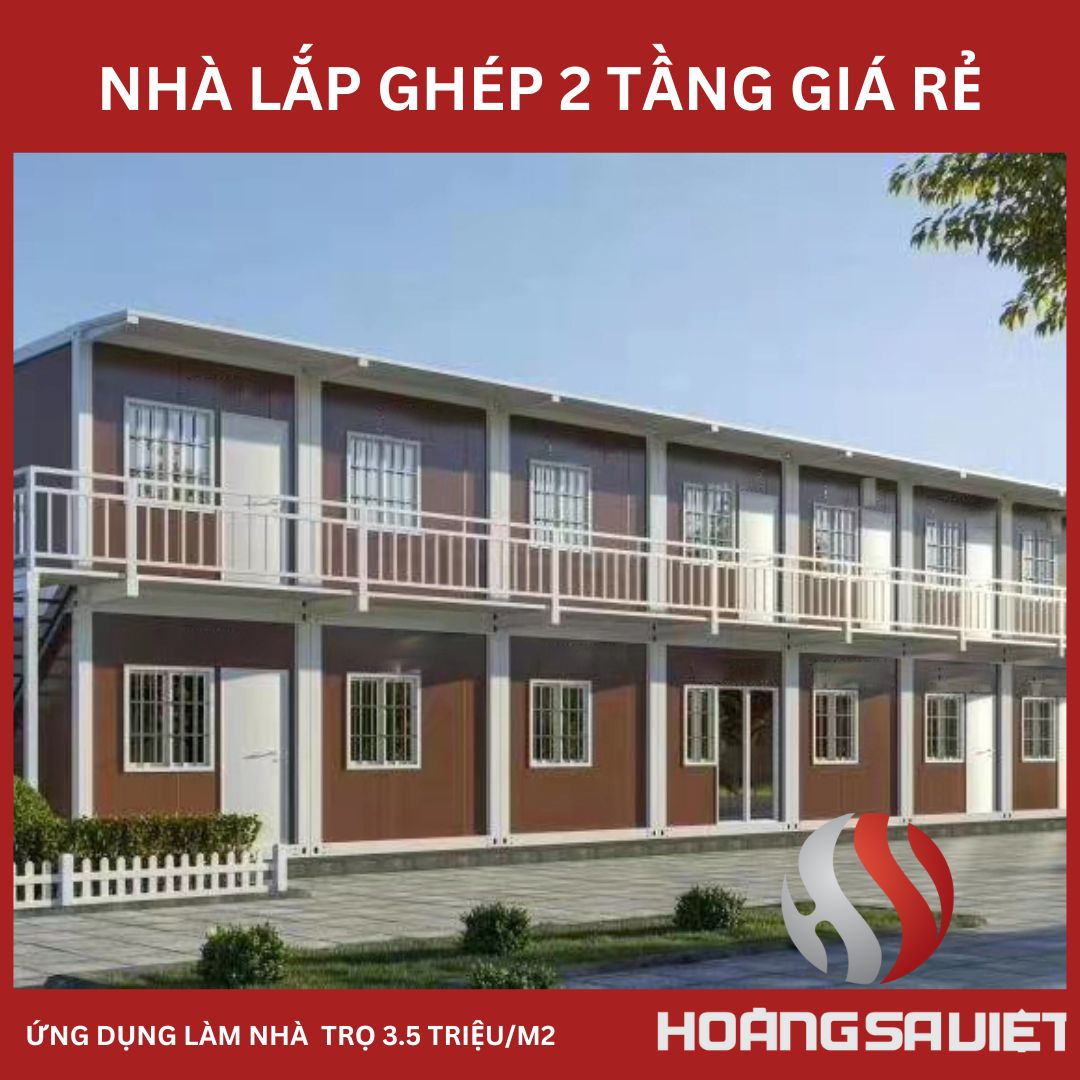
In addition, with the criteria of quick, clean construction and reasonable price, Hoang Sa Viet Construction's 2-storey assembled house design is not only beautiful but also costs only 2/3 of that of house builders. traditional. This helps customers save significantly on costs while still ensuring a comfortable, modern living space. Compared to traditional high-rise buildings, our high-rise prefabricated houses are not inferior in terms of features and aesthetics. Therefore, beautiful 2-storey steel frame houses are increasingly popular and become a popular choice in modern construction projects.
If you are looking for a construction solution that is both cost-effective and ensures quality and aesthetics, let Hoang Sa Viet Construction accompany you. We are committed to bringing you perfect 2-storey prefabricated house models that meet all your requirements and expectations. With experience and reputation in the industry, we are confident that we will bring you a dream home with an ideal and comfortable living space. Let us help you turn your idea of a perfect home into reality.
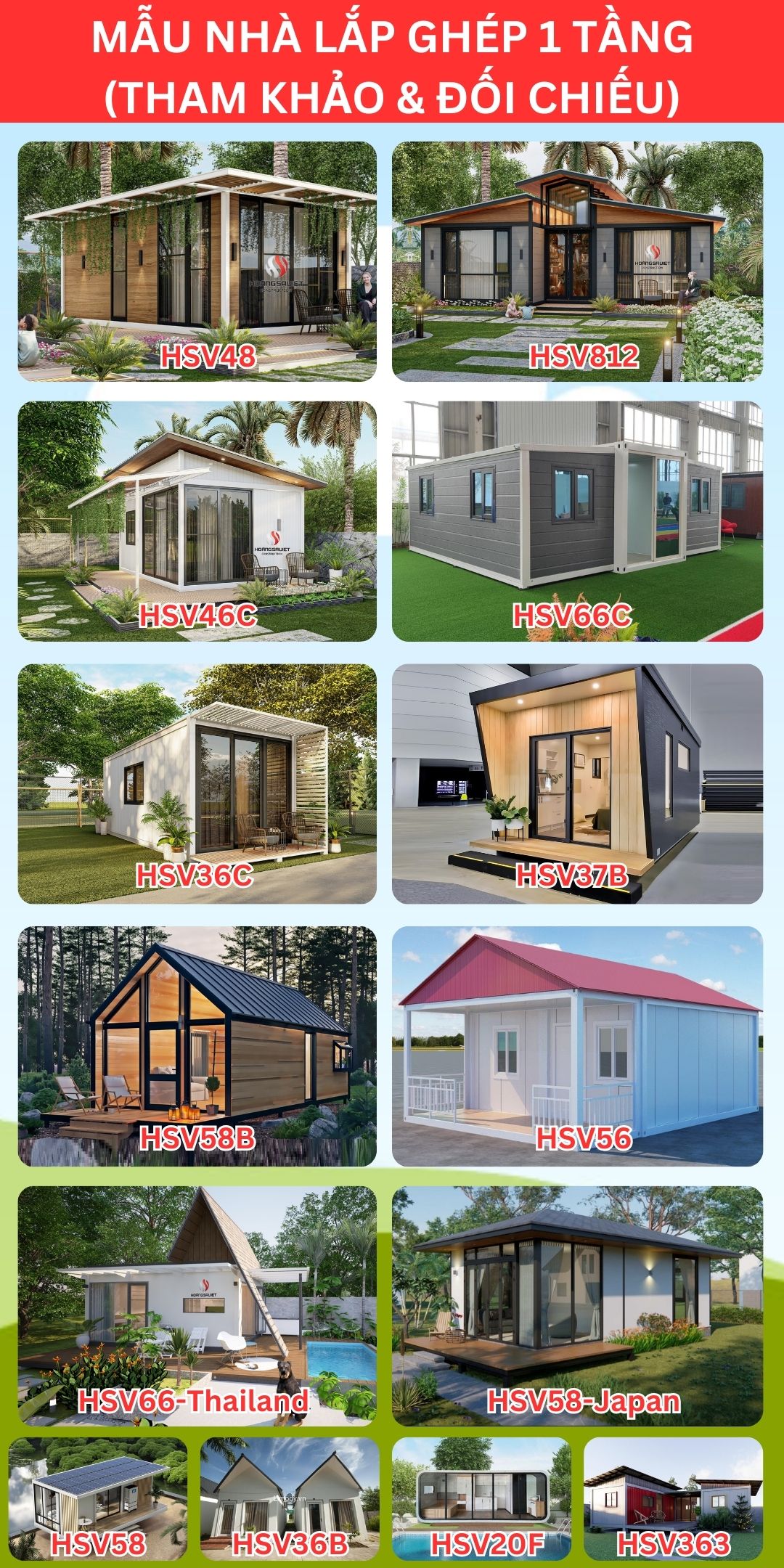
SEE MORE PRODUCTS:
ADVANTAGES OF PREfabricated HOUSES COMPARED TO TRADITIONAL CONSTRUCTION HOUSES
.jpg)
The 2-storey prefabricated house is not only cheap, affordable, and durable, no different from a traditional house, but also has many outstanding advantages suitable for the "fast-moving" era, which can be highlighted. via as:
1. Prefabricated houses protect the environment:
Prefabricated houses are a sustainable and environmentally friendly construction solution, bringing many significant benefits in protecting the living environment. The process of building prefabricated houses helps minimize the amount of dust and waste generated into the environment. Cement panels and composite materials are produced at the factory according to strict environmental protection standards, ensuring to minimize negative impacts on the surrounding environment. This is especially important in the current context, when environmental pollution is becoming a major concern for public health.
Not only stopping at minimizing pollution during construction, prefabricated houses can also be designed to make the most of natural light and save energy, thereby reducing carbon emissions and reducing pressure. force on the energy system. Solutions such as natural ventilation systems, using effective insulation materials and integrating energy-saving devices are important factors that help prefabricated homes become a green and sustainable choice.
2. Prefabricated houses can be flexibly changed in size when needs arise
One of the outstanding advantages of prefabricated houses is the ability to flexibly change size to meet the diverse needs of the family. When the need to expand living space arises, prefabricated houses allow you to easily expand or reduce the area of the house without much difficulty.
In case you need more space for functional rooms such as bedrooms, offices, or common rooms, expansion will become simple and effective. We will add additional modules to your old house, creating a new space while still ensuring aesthetics and solid structure.
Prefabricated houses are designed with separate modules that can be easily connected to each other through specialized accessories such as bolts, screws, etc. This not only helps the construction process expand quickly. but also ensures the safety and sustainability of the house. Adding new modules to an existing house does not require demolition or major structural changes, saving costs and time.
SEE MORE PRODUCTS:
The flexibility in changing the size of prefabricated houses also allows you to easily adjust your living space according to your family's growing needs. For example, when your family has new members or needs a more private space, adding modules will promptly meet usage needs without having to rebuild from scratch. On the contrary, if usage needs decrease, you can narrow the space by removing some modules without affecting the rest of the house.
In addition, changing the size of the prefabricated house also helps you make the most of the available land area. With limited land, you can start with a small house and then expand as needed. This helps you optimize your living space and ensure the house always fits your family's needs and lifestyle.
3. Prefabricated houses are flexible in assembly and relocation:
One of the outstanding features of prefabricated houses is their outstanding flexibility in assembly and relocation. Unlike traditional construction projects, prefabricated houses have the ability to be disassembled and reassembled easily and quickly. This not only saves time and effort during the construction process but also provides maximum flexibility for users.
Finished prefabricated house products can be reused many times while still ensuring high quality and durability. This is especially useful for businesses and individuals who need to use prefabricated houses for many different purposes, from boarding houses, houses for workers, serviced apartments for rent to homestay services. With the ability to reuse, prefabricated houses help reduce initial investment costs and optimize resources.
When relocation is required, prefabricated houses prove to be extremely flexible. You just need to disassemble the frame and walls of the house and transport it to the new location. This process is quick and does not require a lot of manpower or complicated equipment. This makes prefabs the ideal solution for areas that require constant relocation or business location changes.
For boarding houses, houses for workers or serviced apartments for rent, prefabricated houses are a reasonable choice to ensure flexibility and convenience when relocating. When a business expands or moves its business premises, relocating a prefabricated house will not cause many difficulties and costs, and will help maintain business operations continuously and effectively. Similarly, for homestay services, prefabricated houses allow you to easily change your business location to meet seasonal tourism needs or areas with a high number of tourists.
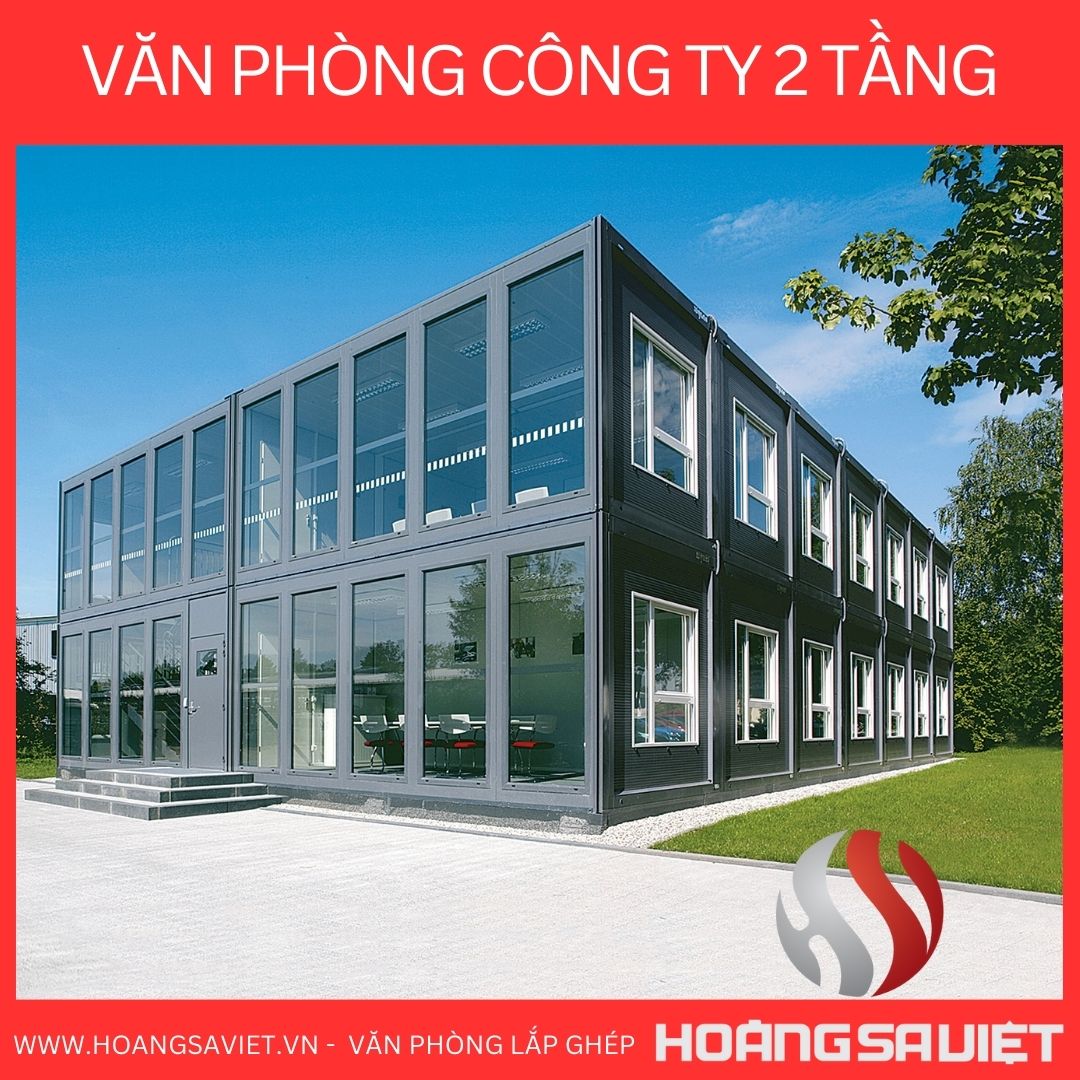
4. Prefabricated houses have high aesthetics:
Prefabricated houses not only stand out for their flexibility and convenience, but also have the ability to bring high aesthetics, meeting all strict design requirements of customers. Built from standard modules, prefab homes can be easily customized to individual needs and preferences, creating a unique and stylish living or working space.
One of the biggest advantages of prefabricated homes is the ability to customize the design. Customers can request a variety of designs to suit their style and purpose. For example, if you want to create a spacious and modern office space, the customer can request a 6m wide glass panel on the entire side, helping to take advantage of natural light and create an airy feeling. Glass not only increases aesthetic beauty but also helps the interior space become brighter and more pleasant.
Besides, to increase modernity and warmth, the floor can be covered with wood, creating a luxurious and intimate beauty. Wood floors not only bring a warm feeling but are also easy to clean and maintain, contributing to improving the quality of life for users. Customers can also choose from a variety of materials and colors to create a vibrant and personalized space.
SEE MORE PRODUCTS:
Prefabricated houses also allow the integration of many different design details to create unique and attractive houses. From the choice of paint color, partition material, to interior details such as windows and balconies, all can be customized to suit each customer's individual preferences and style. This helps create a living or working space that is not only beautiful but also fully equipped and functional.
In addition, prefabricated houses can also be designed to suit many different architectural styles, from modern, classic, to minimalist or industrial. Customers can choose the style that best suits them and create a home with a personal touch. With flexibility in design, prefabricated houses easily meet all requirements and create unique and inspiring living spaces.
5. Prefabricated houses save costs and construction time:
Prefabricated houses are not only a modern solution but also bring many benefits in terms of cost and construction time. With a simple assembly process and few complicated operations, building prefabricated houses becomes much faster and more effective than traditional construction methods. In just one day, we can complete the assembly of a house, ready for you to use immediately.
The first highlight of prefabricated houses is the ability to save construction time. Because the parts of the prefabricated house are already manufactured at the factory, the work at the construction site is mainly just assembling the modules together. This process is not only quick but also minimizes risks and errors that may occur during construction. With prefabricated houses , you don't need to wait months to have a completed house. This is especially useful in situations where emergency housing is needed or when you want to get settled quickly.
Not only does it save time, prefabricated houses also help reduce costs significantly. Because the assembly process is quick, you will save on labor costs, one of the largest expenses in construction. Furthermore, because there is no need to dig deep foundations and many complicated steps, costs incurred during construction are also significantly reduced. Prefabricated houses use pre-produced materials, which are cheaper than using traditional construction materials, helping to reduce total construction costs significantly.
Saving costs and time not only helps you get a house quickly but also helps you manage your budget more effectively. With prefabricated houses , you can accurately estimate construction costs from the beginning, avoiding unwanted costs arising during the construction process. This is especially important for families with limited budgets or projects that need to be completed quickly.
6. Prefabricated houses have better sound and heat insulation than conventional prefabricated houses.
Prefabricated houses not only bring benefits in terms of cost and construction time but also excel in soundproofing and heat insulation, compared to conventional prefabricated houses. The wall system is installed with high quality panels, combined with a corrugated iron roof with mineral wool insulation, ensuring a quiet and cool living space.
Using panels for partitions not only helps reduce the weight of the project but also enhances sound insulation. The panel is made from layers of specialized materials, capable of effectively absorbing sound, minimizing noise from outside. This is especially useful when prefabricated homes are located in areas with high population density or near busy traffic routes. With a soundproof wall system, you can enjoy a quiet, relaxing living space without being affected by surrounding noise.
SEE MORE PRODUCTS:
The insulation ability of prefabricated houses is also significantly improved thanks to the mineral wool insulation layer in the corrugated iron roof. This layer of mineral wool has the function of hindering heat transfer, keeping the space inside the house cool in the summer and warm in the winter. This not only brings comfort to residents but also helps save energy, reducing electricity costs for air conditioning systems. With an effective insulation system, prefabricated houses become an ideal solution for hot or cold climates.
Not only stopping at soundproofing and heat insulation, panels and insulation materials are also designed to be fireproof, increasing the safety of the house. In case of fire, these materials will limit the spread of fire, protecting your life and property. This is especially important in areas with high risk of fire or explosion or when prefabricated houses are used as offices or factories.
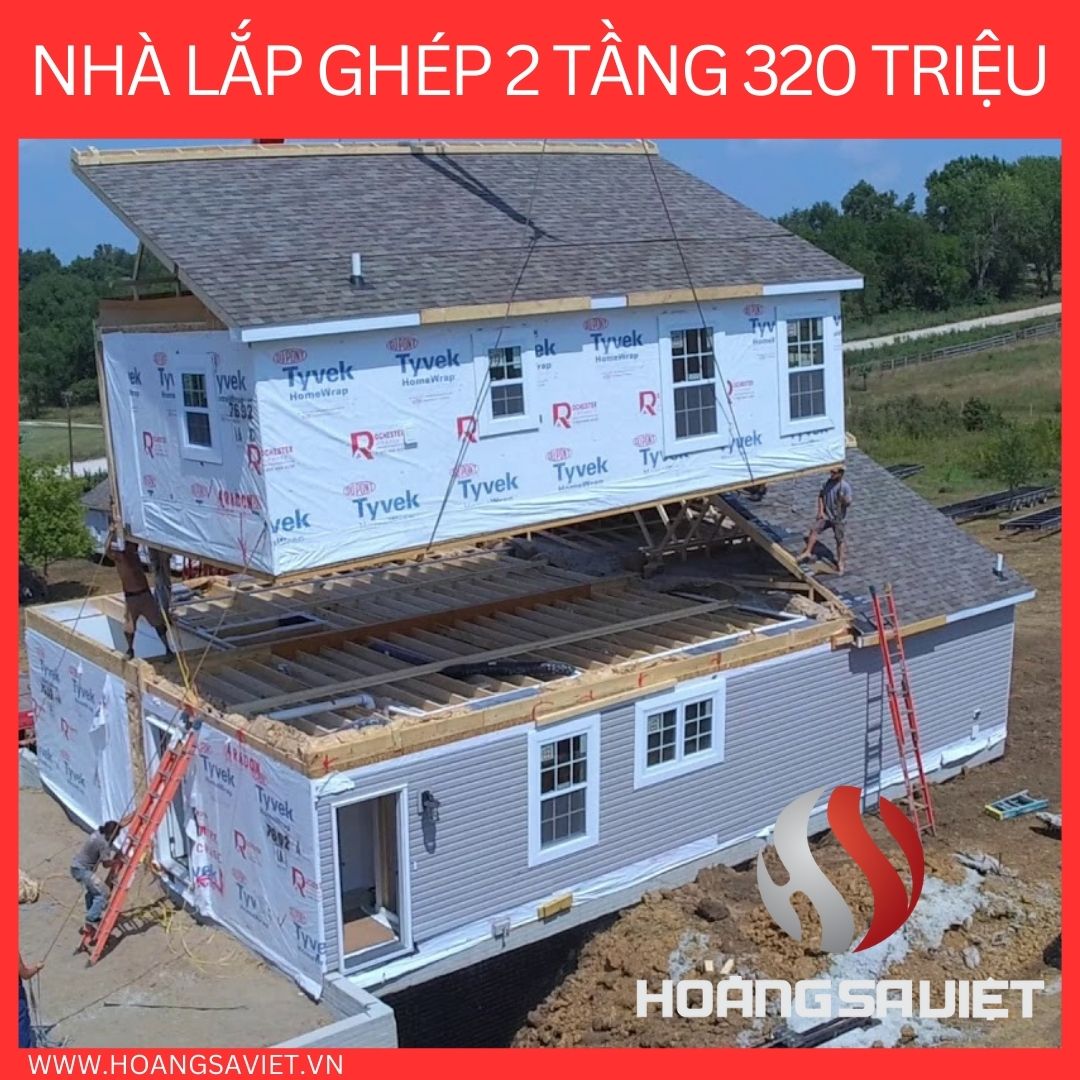
7. Prefabricated houses are easy to liquidate and rent:
Prefabricated houses not only stand out with many advantages in terms of cost, construction time and sound and heat insulation capabilities, but also provide outstanding flexibility when you need to liquidate or rent. One of the biggest benefits of the prefabricated house model is the ability to liquidate easily and quickly. When you no longer need it, you can easily sell the house to companies or individuals in need.
Many companies and businesses today are very fond of the prefabricated house model because of the flexibility and cost savings it brings. Therefore, when you want to liquidate, you can resell it to companies looking for temporary accommodation solutions or office space expansion. Even suppliers of assembled products often need to purchase these products for reuse or repair, creating favorable conditions for liquidation.
In addition to liquidation, prefabricated houses are also a great choice for a rental business model. You can rent prefabricated houses to companies to use as offices, worker housing, or temporary accommodation. This not only helps you recover your investment quickly but also creates a stable source of income from rentals. With the ability to easily relocate and quickly assemble, prefabricated houses are an ideal solution for businesses that need a space that is flexible and can be converted according to needs.
The flexibility in liquidation and leasing of prefabricated houses helps optimize investment value and meet the needs of many different customers. With this feature, prefabricated houses are not only a cost- and time-saving solution but also bring diverse and favorable business opportunities. Consider using a prefabricated house to take advantage of these benefits and maximize the value of the house during use.
8. Quality management:
Prefabricated houses offer a smart construction solution with outstanding quality management capabilities thanks to the use of modern Smartboard cement panels. These cement panels are mass produced with advanced technology, helping to control construction quality effectively and synchronously. This not only minimizes problems related to gutting the project but also saves costs in an optimal way.
With prefabricated homes, each component is manufactured and quality tested right from the production stage, ensuring that materials meet the highest standards before being assembled. Smartboard cement panels, with good moisture and fire resistance, contribute to minimizing unsatisfactory construction and ensuring the durability of the project.
Besides, prefabricated houses also stand out with excellent sound and heat insulation, thanks to the use of advanced materials and technology in the production process. Smartboard cement panels and other insulation materials help keep interior spaces comfortable and welcoming, minimize outside noise and save energy.
The structure of the prefabricated house is made of light steel, helping to reduce the load of the project while still ensuring safety and stability. This not only helps reduce construction costs but also ensures that prefabricated homes always meet design and safety standards.
Thanks to strict quality management and the use of advanced materials, prefabricated homes are not only a cost-effective option but also ensure sustainability and outstanding performance throughout their lifetime. .
SEE MORE PRODUCTS:
9. Prefabricated houses are always manufactured 100% new:
When compared to container houses, prefabricated houses stand out by being 100% newly manufactured, ensuring origin, quality and peace of mind for users. Prefabricated house products are manufactured in factories according to strict quality standards, from new materials, helping to ensure the integrity of the project and the safety of users. This not only brings peace of mind in terms of quality but also better meets the needs of spirituality and comfort in the living space.
In contrast, container houses are often used containers of goods, which are resold at a lower price. These containers have spent a long time transporting many different types of goods, and it is difficult to clearly determine their origin and condition. Reusing old containers can pose a health risk because they may contain toxic chemicals or materials that are no longer of good quality.
Therefore, choosing a 100% new prefabricated house not only ensures outstanding quality but also brings absolute peace of mind and safety to users. Using new products, made from standard materials, is a smarter choice when you put quality and safety first in building a living or working space. .
(Erection of a 2-storey prefabricated house as a showroom and office)
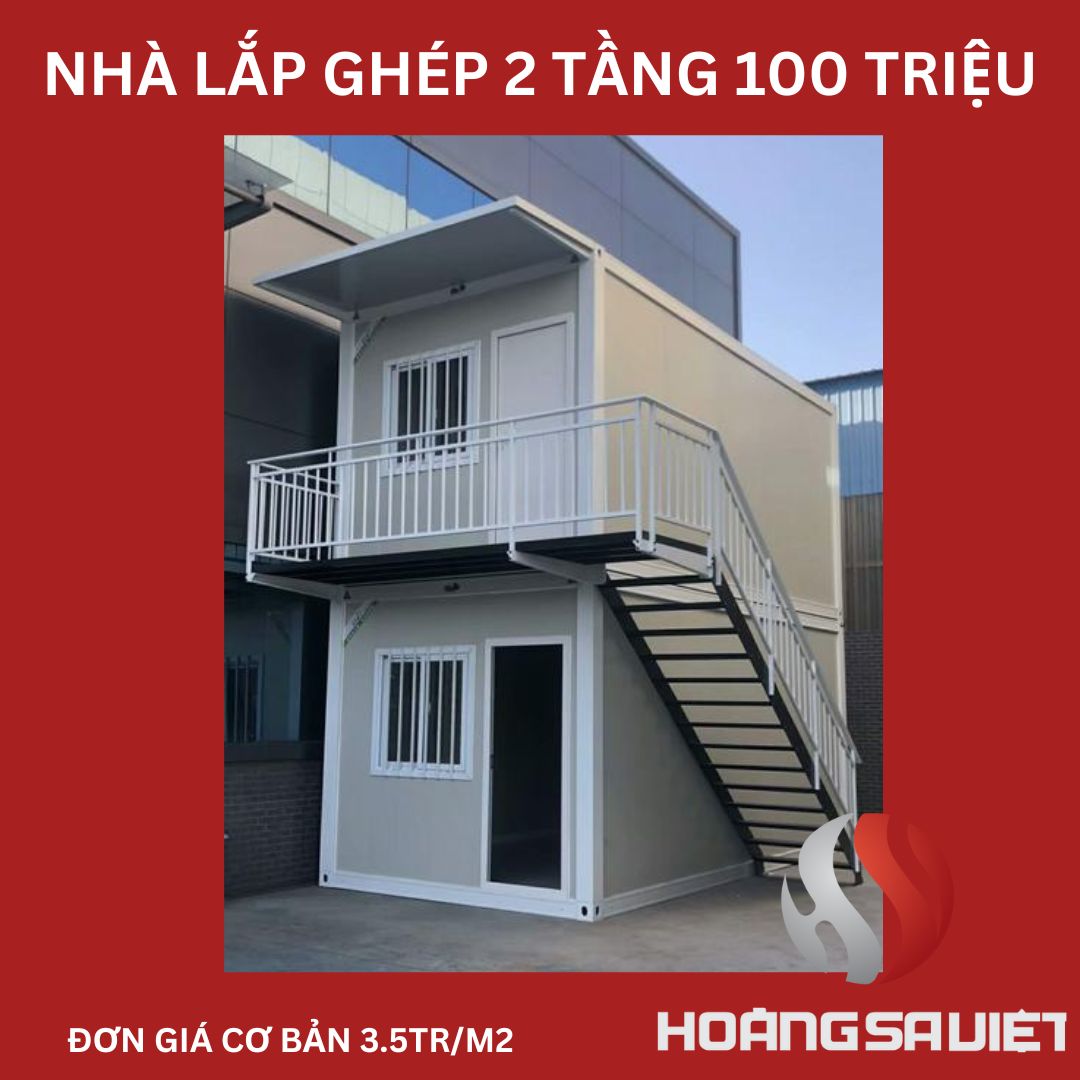
HOW IS THE PRICE OF A 200 MILLION 2-STORY ASSEMBLY HOUSE CALCULATED?
Determining the cost of building a 2-storey prefab house depends on many factors, including materials, labor and other incurred costs. The cost of prefabricated houses is usually calculated on a unit price per square meter (m2), and may vary depending on additional requirements such as interior decoration, sanitary system installation, and other amenities. .
For a budget of about 200 million VND, you can build a 2-storey prefab house with an area of about 50-60m2. Specifically, each floor of the house will have an area of 24-30m2, allowing you to design a comfortable and reasonable living space.
The valuation of construction costs will be adjusted based on the specific requirements of the project, including the quality of materials used, labor required and special design requirements. In addition, factors such as the installation of interior equipment, electrical and water systems, and other additional costs also need to be carefully considered to ensure that your construction project is carried out properly. most effective and optimal.
For building 2-storey prefabricated houses:
1. Flatten the foundation (place the 2-storey prefab house on top)
Making the foundation for a 2-storey prefab house is clearly different from building a traditional house, thanks to the flexibility and simplicity of this construction method. One of the biggest advantages of prefabricated houses is the ability to build on many different types of terrain without requiring a complicated foundation.
For hard ground , the foundation construction process is much simpler. Just level the ground and pour a layer of concrete 10-20cm thick, with a layer of D100-D200 woven iron to enhance durability. After the concrete layer has dried, it can be rolled flat to line ceramic tiles or plastic wood. This process does not require foundation beams, helping to reduce construction costs and time.
For soft ground , some additional preparation steps are needed. First, pour debris or rocks onto the surface, then use a roller to compact the soil layer to ensure the necessary hardness. Because the tonnage of a 2-story house is only 3-4 tons, evenly distributed over an area of 36 square meters or more, the house's impact on the foundation is very small, equivalent to placing a container on a flat floor. .
The cost for leveling the floor and pouring concrete ranges from 500,000 VND to 1 million VND per m2, depending on the specific ground conditions. The foundation construction process for a 2-storey prefab house is not only simple but also cost-effective, helping you easily calculate and prepare the budget for your construction project.
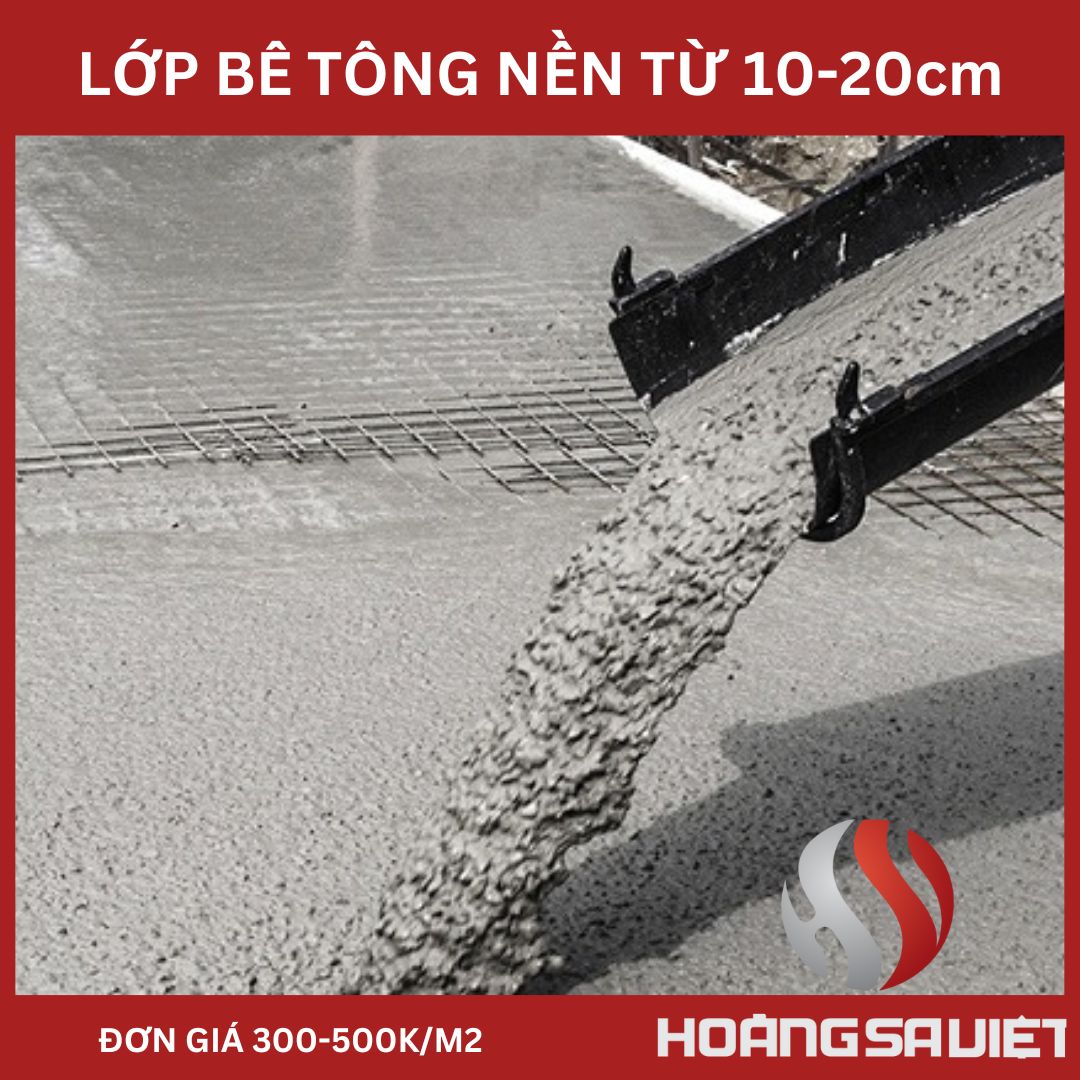
2. Make septic tank and septic tank systems for compound houses
When building a prefabricated house , installing a septic tank and septic tank system is an important part to ensure comfort and hygiene for the house. For modern prefab house models, this system is designed quite simply and conveniently, thanks to the development of modern construction materials.
Prefabricated house septic tanks and septic systems are often implemented with composite plastic septic tanks, an effective and cost-effective solution. These septic tanks are available on the market and are very easy to use. You just need to choose a septic tank that suits your needs, then bury it underground at the appropriate location. The cost of purchasing and installing a septic tank usually ranges from 5-7 million VND, depending on the size and type of tank.
SEE MORE PRODUCTS:
If you have the ability to do it yourself or hire a worker, you can save an additional 1-2 million VND for installation. To optimize costs and effort, buy a septic tank from dealers near your area. Choosing a location to bury the septic tank near the toilet area will help save costs on wastewater pipes, while minimizing installation work.
After the septic tank is in place, it is necessary to lead the wastewater pipe from the toilet to the discharge area. This helps ensure the wastewater treatment system operates effectively and maintains the house's hygiene.
3. Costs for making gates, yards and landscapes.
When building a prefabricated house, the design and construction of the gate, yard and surrounding landscape is very important to perfect the living space and create a harmonious appearance for the house. Depending on location and specific requirements, costs for these items can vary significantly.
For houses built in rural areas or large areas, building gates, yards and landscapes can be done quite simply. You can hire a team of builders to do these jobs yourself.
The cost of building yards and roads usually ranges from 500,000 VND to 1,000,000 VND/m². For gate construction , depending on the material and design, the cost can range from 1,000,000 VND to 1,500,000 VND/m².
In addition to making gates and roads, you can enhance the beauty of the grounds around the house by buying ornamental plants, making stone steps leading to the entrance, planting grass and designing miniature landscapes. These elements not only increase aesthetics but also create a cool green space, close to nature.
By investing properly in the design of gates, yards and landscapes, you not only enhance the aesthetic value of your home but also create a pleasant and relaxing living environment.
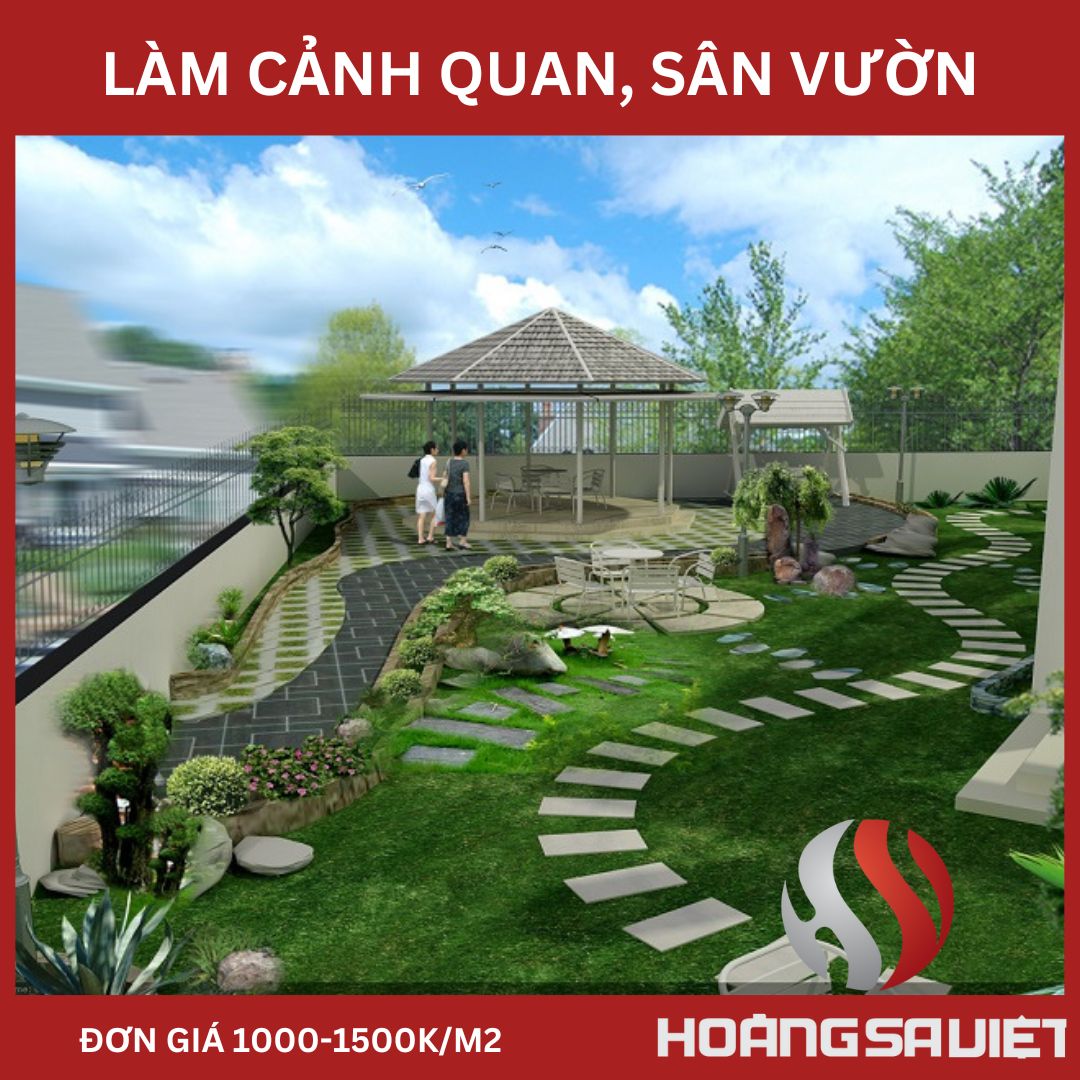
4. Cost of assembling the houses (frame _ walls _ floor)
When building a prefabricated house , the cost will depend on the size and number of houses that need to be assembled. A prefabricated house is usually made up of many houses with standard sizes such as 3m x 5m, 3m x 6m or 4m x 6m. Depending on the configuration and specific requirements, the average cost for assembling each m² of the house usually ranges from 3,000,000 VND to 3,500,000 VND.
To illustrate, if you build a house with a total area of 78m², the assembly cost will be calculated as follows: 78m² x 3,200,000 VND = 249,600,000 VND. Depending on specific requirements and other factors, this cost can fluctuate around 200 million VND.
Assembly of the pavilions includes the installation of frames, walls and floors, all of which are carried out on site in a quick and efficient manner. This not only helps save construction time but also reduces costs incurred compared to traditional construction methods.
By calculating assembly costs based on area and other factors, you can effectively plan your budget for your prefab home construction project.
5. Furniture assembly costs
When completing a prefabricated house, the cost of interior assembly is an important part that needs to be carefully calculated. To ensure the house is both comfortable and beautiful, interior installation will include many different items with specific costs.
- Install Tempered Glass: If the house is designed with a lot of tempered glass, the cost will vary depending on the area and style of the glass. Tempered glass often costs more than regular glass, but brings luxury and durability to the home.
- Installing Sanitary Equipment: The cost of installing sanitary equipment usually ranges from 10,000,000 VND to 15,000,000 VND for each toilet. This includes basic equipment such as toilets, sinks, showers and other accessories.
- Installing Kitchen Cabinets: Kitchen cabinets are an important part of kitchen furniture, and the cost of installing kitchen cabinets is usually from 10,000,000 VND to 30,000,000 VND per cabinet. This price will depend on the size, material and design of the kitchen cabinet.
- Other Furniture Items: In addition to the main items, there are many other items such as beds, wardrobes, TV shelves, sofas, study desks, and other decorative items. The cost of these items will vary depending on the brand, material and design you choose.
Total interior assembly costs can vary based on personal needs and preferences, along with the size and design of the home. By detailed planning and choosing the right products, you can ensure that your prefabricated house will fully meet your aesthetic and functional requirements.
SEE MORE PRODUCTS:
DO I NEED A PERMISSION TO BUILD A 2-STORY ASSEMBLY HOUSE FOR 200 MILLION?
A 2-storey prefabricated house , although it is a high-end prefabricated house, still must comply with legal regulations when used as a long-term residence. According to current regulations, if you use a container house to live, applying for a construction permit is required. This is to ensure the home meets safety standards and building regulations.
However, in the case of using a 2-storey prefabricated house for temporary purposes such as a mobile office or accommodation for workers serving a specific project, a construction permit may not be necessary. These structures are often temporary in nature, and regulations may vary depending on locality.
Because the characteristic of prefabricated houses is that they can be easily assembled and disassembled, this model offers more flexibility than traditional houses. For example, in remote areas such as mountains, coastal areas, or areas serving activities such as farming or aquaculture, prefabricated houses can be built quickly without much trouble. legal obstacle.
However, building a small house without a permit is often more sympathetic to the authorities, but this still depends on the specific regulations of each locality. Therefore, before proceeding with construction, you should carefully study local legal regulations to ensure compliance with regulations and avoid unwanted legal risks.
See more products of Hoang Sa Viet:
REFER TO CHEAP 2-STORY ASSEMBLY HOUSE MODELS
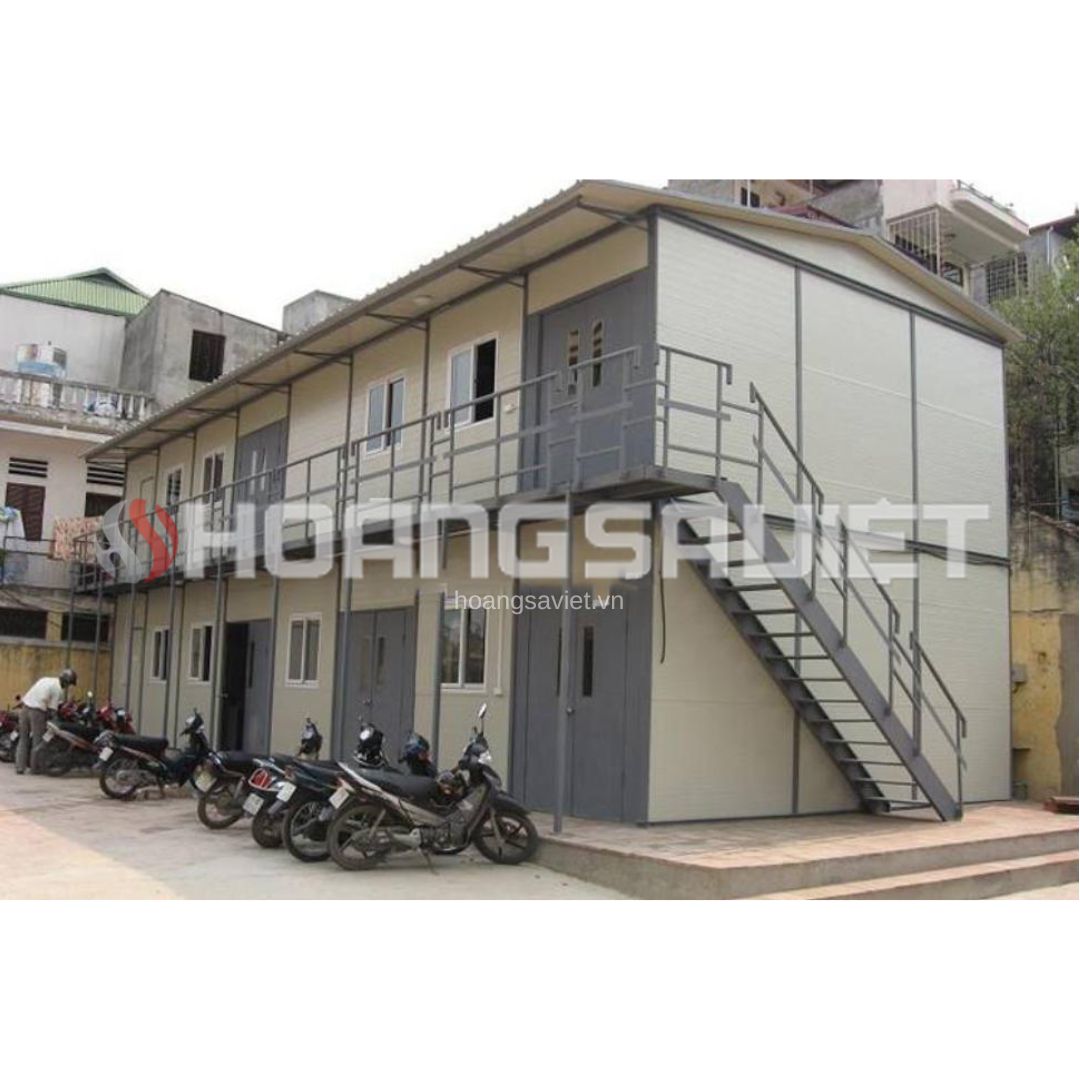
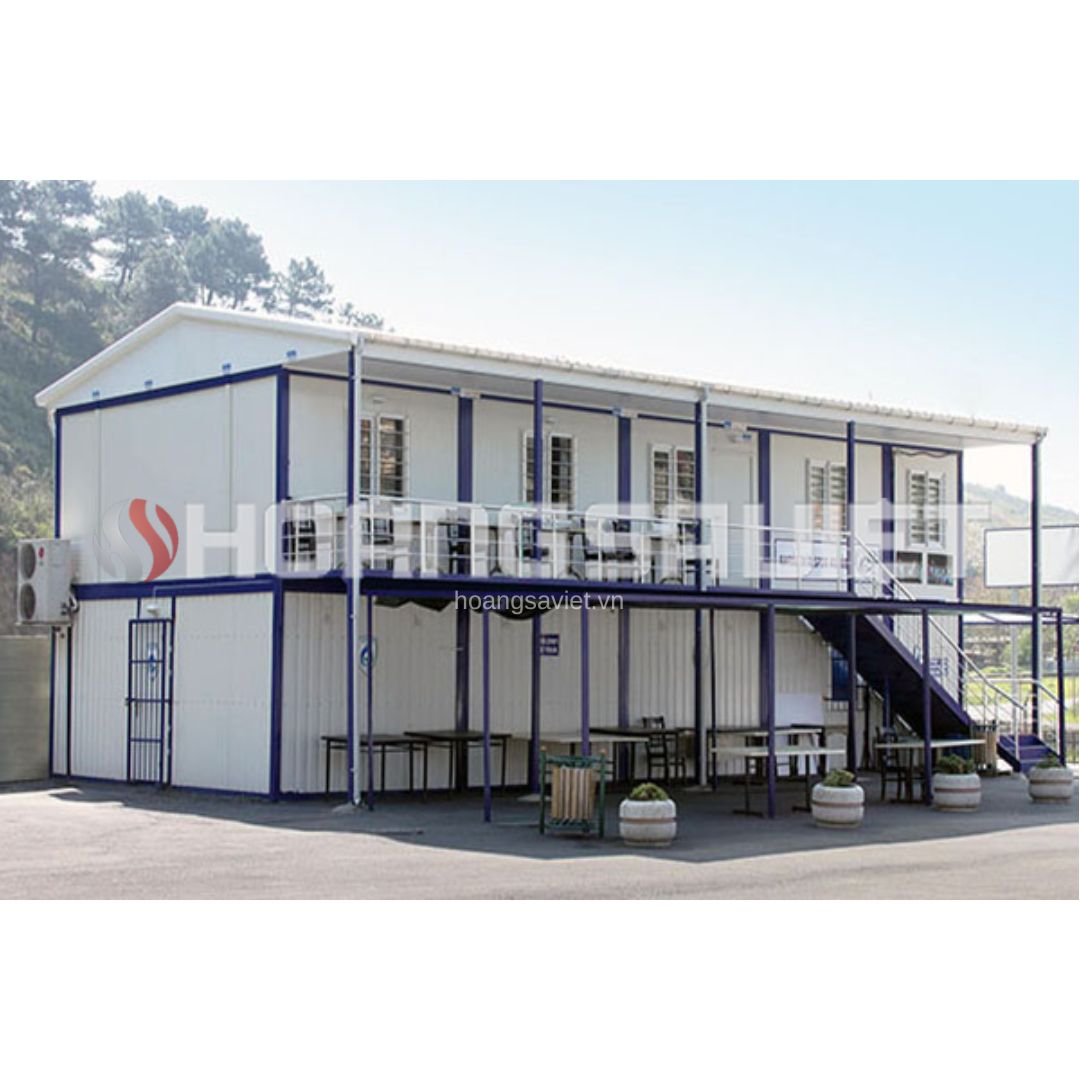
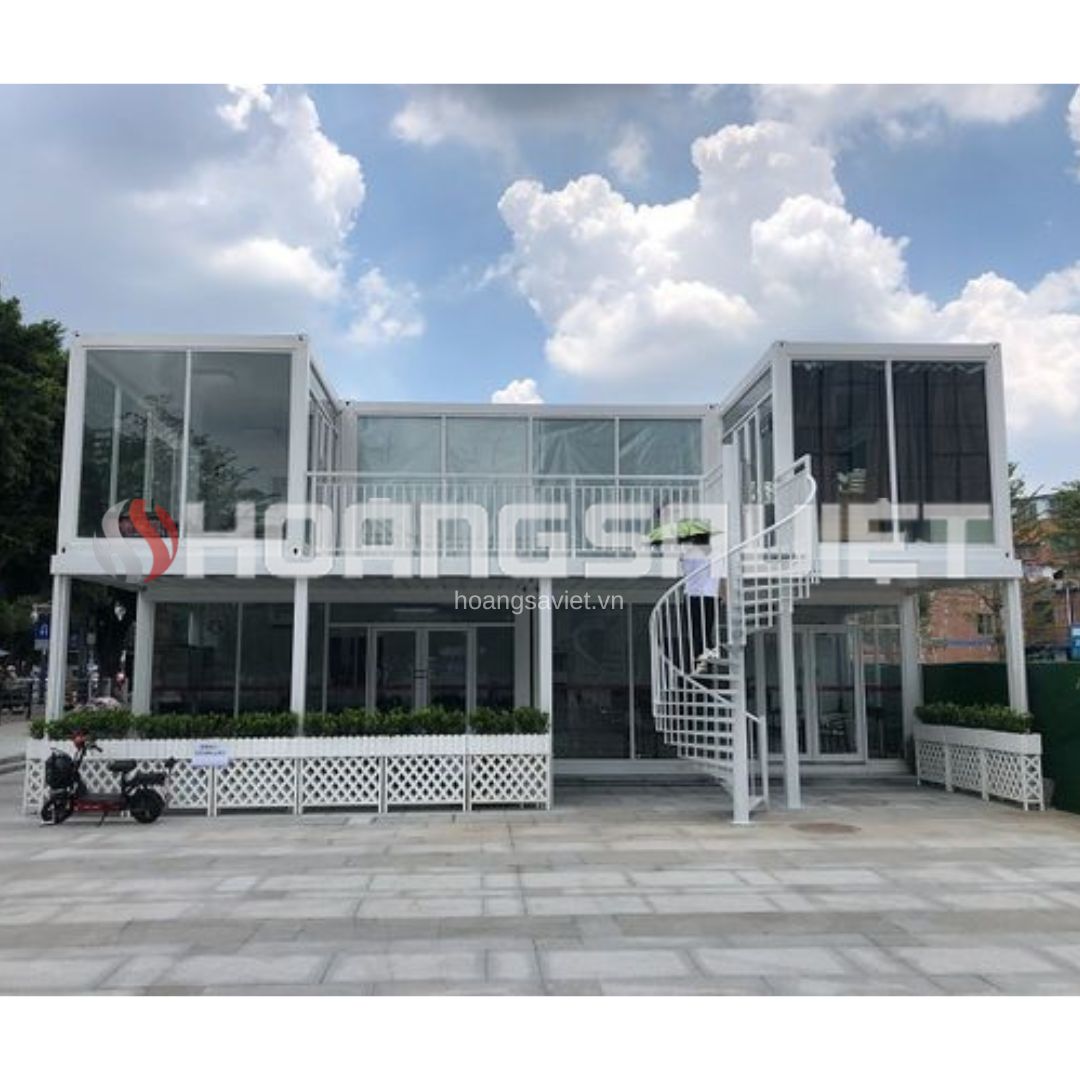


content

content
e